Recycling Products
More recycling equipment to meet your needs
Plastic washing and recycling system CAD drawing reference
Different projects, different configurations.
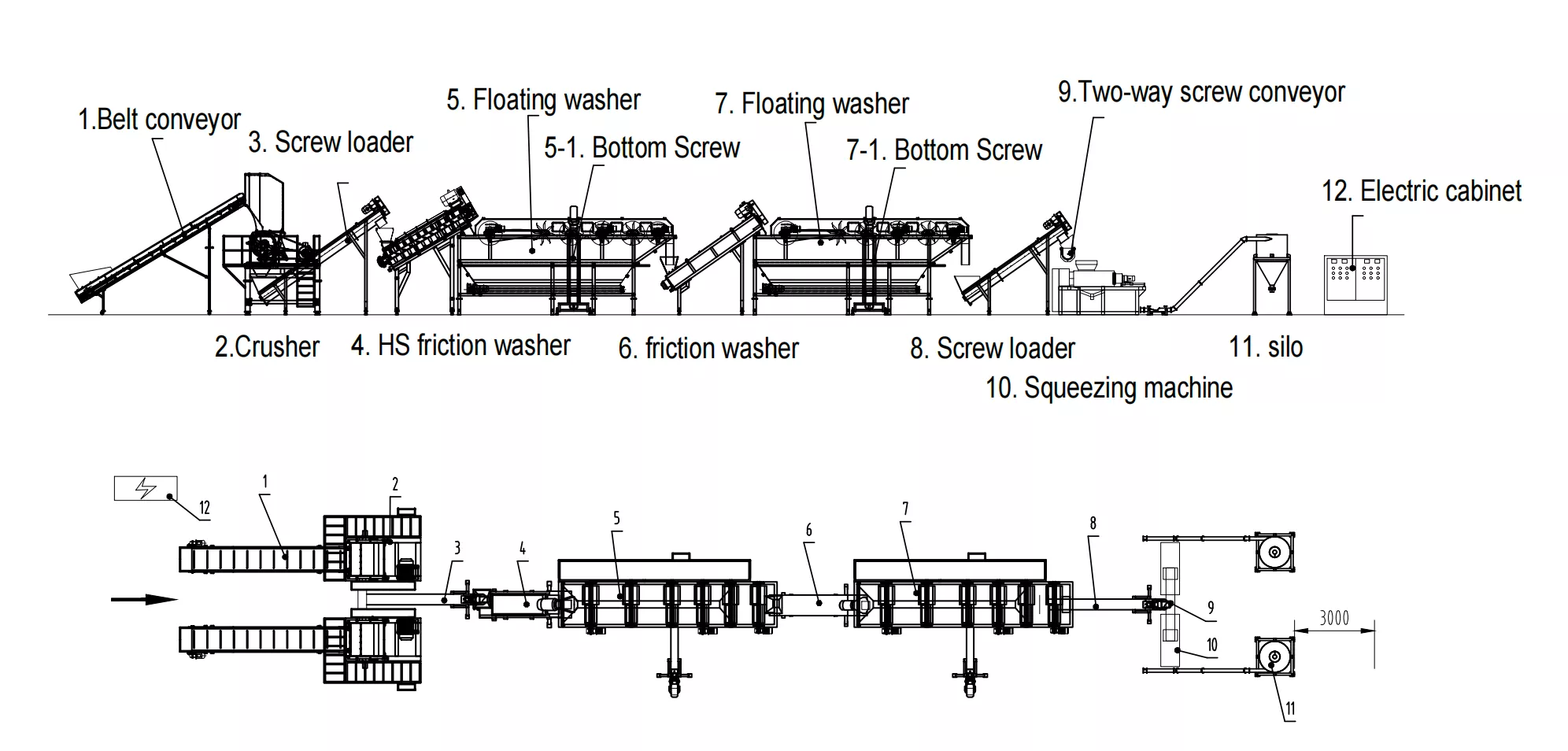
Get Plastic Recycling Machine Solutions
OUR SKILL
Our Simple & Transparent Process
Whether you require a single machine, a turnkey recycling plant, or a bespoke solution, we guarantee top-tier customer service and communication for efficient project execution.
Step 1: INQUIRE NOW
Reach out to us with any questions about our machinery, washing lines, or custom projects.
Step 2: SPECIFICATION CONFIRMATION
We'll work closely with you to confirm every technical detail and ensure the machine perfectly meets your requirements.
Step 3: QUOTATION
We'll provide you with our most competitive quote and delivery time for your consideration.
Step 4: SIGN CONTRACT
If you're prepared, let's sign the contract to initiate the manufacturing process.
Step 5: INVOICE & DEPOSIT
Once the contract is signed, we will issue an invoice for the initial 30% deposit to commence the project.
Step 6: MANUFACTURING
Depending on the project size, our typical lead time ranges from 30 to 90 days.
Step 7: INSPECTION
Either visit us for an in-person inspection or opt for a virtual assessment via video call.
Step 8: SHIPMENT
Upon completion of the final payment, your machine will be prepared for immediate shipment.
Plastic Recycling Machine Blogs
Insights and Updates on Recycling Technology
Stay informed with our latest blog posts covering a wide range of topics in the plastic recycling industry. From innovative machine designs to best practices in recycling processes, our blogs offer valuable insights for both industry professionals and environmental enthusiasts.
1200+ Happy Clients
The performance of the HDPE washing line has been exceptional, boosting our output by over 30%. What impressed us most was the post-installation support; their team was knowledgeable and responsive, ensuring a smooth integration into our existing workflow.
Outstanding recycling equipment! The washing machine's efficiency has transformed our plastic processing capabilities. The build quality is exceptional and the automated features have significantly reduced our labor costs while improving output quality.
Incredible ROI on this plastic recycling system! Within 8 months, we recovered our investment through improved efficiency and reduced waste disposal costs. The technical support team deserves special recognition for their expertise and dedication.
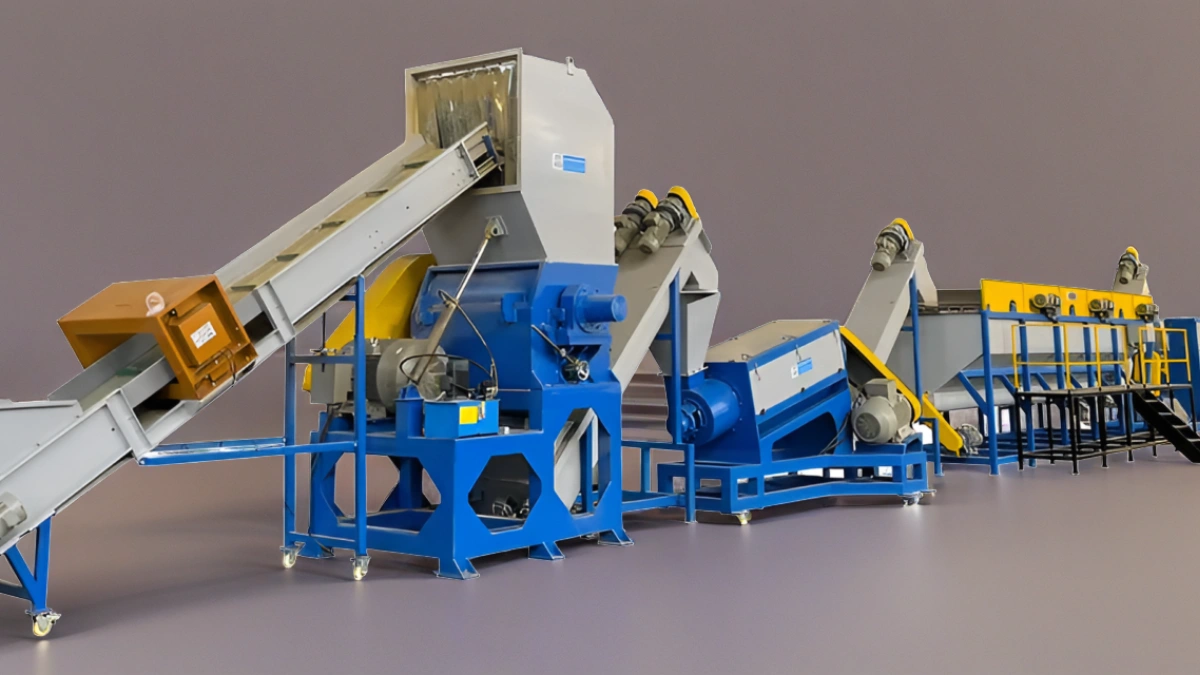
Latest From Media
Stay Informed with Our Device Videos
Waste plastic bottles wet crusher
HDPE Recycling Washing Line
PP Woven Bag Shredder & Pelletizing Line
Frequently Asked Questions
Get answers to the most common questions about our Plastic Recycling Machines and how they can benefit your operations.
We’re dedicated to delivering top-tier recycling machinery that combines efficiency, durability, and value. We understand the significant investment involved in purchasing recycling equipment, which is why we’re committed to excellence in every aspect. We invite you to visit our factory and experience our commitment firsthand.

How much do your recycling machinery cost?
To provide you with the most accurate and fair pricing, we customize each quote based on specific needs, shipping rates, and local requirements. Please contact us directly for a detailed quotation.

- Standard machines: Approximately 30-45 days post-contract.
- Plastic Recycling&Washing lines: Between 60 to 90 days.
- Custom projects: Timeline specified in the contract.

Our ordering process is straightforward. Contact us with your equipment needs and any custom specifications. Discover more about our ordering process and how we can assist you in making the best choices.

Yes, we highly encourage testing. For complete systems, we perform a comprehensive trial run before shipment. We invite you to participate in this crucial phase to ensure the machinery meets your standards.

offers a comprehensive one-year warranty on all machines and parts, ensuring they are free from defects.

Yes, we provide a full installation package.
Our certified engineers will assist with the setup and commissioning of your machinery. the client is responsible for arranging and covering travel and accommodations for our engineers. Installation duration varies by project size, typically requiring 7-14 days.