Two-Stage Plastic Pelletising Machine
Transforming rigid PP & HDPE flakes into high-purity, reusable pellets for premium manufacturing applications.
Request a QuotationEngineered for Excellence
Our pelletising system is designed for superior efficiency, quality, and reliability, ensuring you get the maximum value from your recycled materials.
High-Quality Pellet Output
Produces uniform, dense, and thoroughly degassed pellets ideal for injection moulding and other high-end uses.
Automated & Stable Feeding
VFD-controlled screw conveyors ensure a consistent material feed, automatically adjusting to prevent blockages and ensure smooth operation.
Advanced Two-Stage Filtration
A dual-extruder design with segmented filtration removes coarse and fine contaminants, reducing filter changes and maintenance downtime.
Efficient Degassing & Drying
A “dual-zone” vacuum system and advanced dewatering technology effectively remove moisture and volatiles for superior plastic quality.
From Flake to Finished Pellet
A seamless, four-step process that guarantees the conversion of plastic waste into a valuable manufacturing resource.
1. Consistent Feeding
Washed flakes are fed into the system via an automated, speed-controlled screw conveyor.
2. Plasticisation & Degassing
The material is melted in the first extruder, with volatiles and moisture removed by a dual-zone vacuum system.
3. Melt Filtration
Melted plastic is pushed through a two-stage filtration system in the second extruder to remove all impurities.
4. Pelletising & Drying
The pure polymer is cut into uniform pellets by a water-ring pelletiser and dried, ready for packaging.
Technical Excellence in Detail
Every component is engineered for performance and longevity. Explore the key features that set our machine apart.
Key Component Functions
VFD Screw Conveyor
Provides precise, automated control of the material feed rate, optimising the extruder’s performance and preventing overloads.
Primary Single-Screw Extruder
Dedicated to meticulously melting and homogenising the plastic flakes while performing initial degassing and coarse filtration.
Secondary Single-Screw Extruder
Further plasticises the material and uses a high-mesh filter to eliminate fine contaminants, ensuring final pellet purity.
“Dual-Zone” Vacuum Degassing
This innovative system on the primary extruder efficiently removes volatiles, inks, and moisture, crucial for producing high-quality pellets.
Water-Ring Pelletiser
A robust and reliable die-face cutting system that transforms the molten plastic into uniform granules with high efficiency.
Centrifugal Dewatering System
Combines a vibration sieve with a horizontal centrifugal dryer to rapidly remove surface water, preparing pellets for immediate use.
Technical Parameters
Parameter | Specification |
---|---|
Model | TSS-300 | TSS-500 | TSS-800 (Customisable) |
Applicable Materials | Rigid PP, HDPE, HIPS, ABS Flakes (<12mm) |
Output Capacity | 300-1000 kg/h (Varies by model and material) |
Primary Extruder Screw Diameter | 120mm – 180mm |
Secondary Extruder Screw Diameter | 110mm – 170mm |
Main Motor Power | 90kW – 250kW |
Degassing System | Dual-Zone Vacuum Degassing System |
Filtration Method | Two-Stage Plate-Type Hydraulic Screen Changer |
Pelletising Method | Die-Face Water Ring Pelletising |
Cooling Method | Water Cooling |
All product specifications can be customised according to customer requirements.
Equipment Showcase
View our pelletising machine in detail and see it in action.

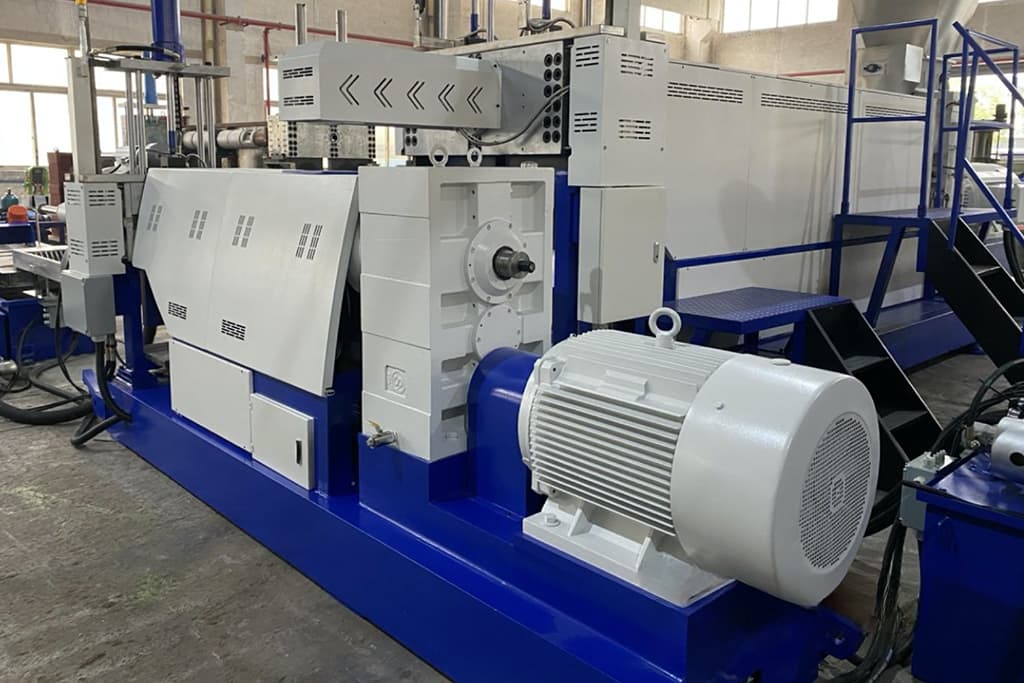
Watch the Machine in Operation
Get a Customised Solution & Quotation
Our team is ready to help you configure the perfect system for your specific needs. Send us a message to get the latest prices, lead times, and technical advice.
Frequently Asked Questions
This machine is primarily designed for pelletising washed rigid plastic flakes, including PP (polypropylene) and HDPE (high-density polyethylene). It can also be adapted for other rigid plastics like HIPS and ABS. For heavily contaminated or printed materials, our two-stage system is particularly effective.
A two-stage system offers superior degassing and filtration. The first extruder melts the plastic and removes most volatiles, while the second extruder refines the melt and performs fine filtration. This results in higher quality pellets with fewer impurities and “voids,” and it also reduces the frequency of filter changes, leading to less downtime.
Yes, we offer comprehensive support services. This includes optional on-site installation, commissioning, and operational training for your team to ensure you can operate the machinery safely and efficiently from day one.
All our new recycling machines come with a 1-year limited warranty, covering parts and manufacturing defects. We also provide ongoing technical support and spare parts services to ensure the long-term performance of your investment.