
PP regrind
It’s common to see them as plastic chairs, toy parts, baskets, trash cans, pipes, bottles, bottle caps, and others because they provide stronger protection for goods.
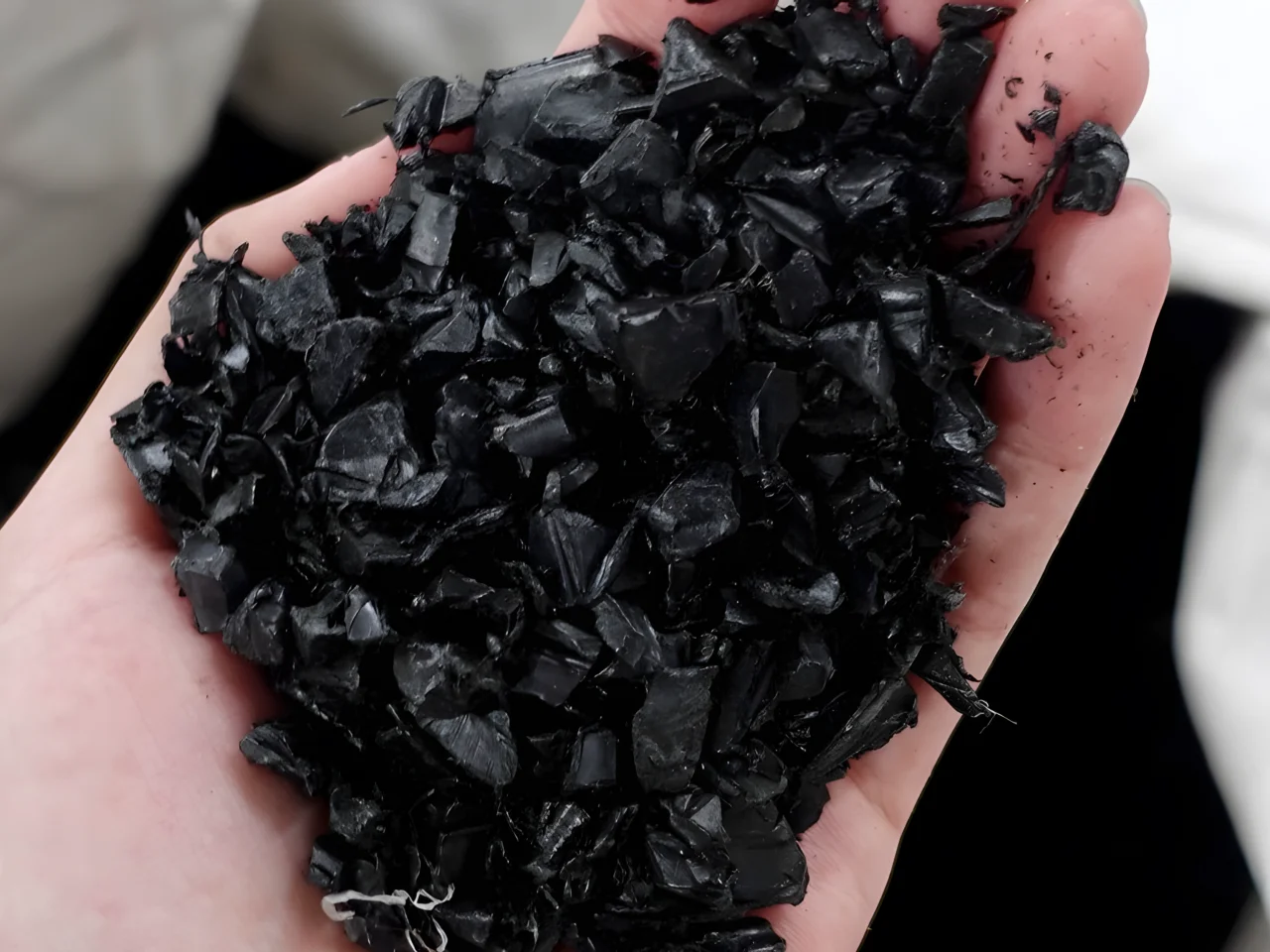
HDPE regrind
HDPE regrind is widely used in containers, plastic bottles, pipes, playground equipment, and more due to its high strength, impact resistance, and chemical durability.
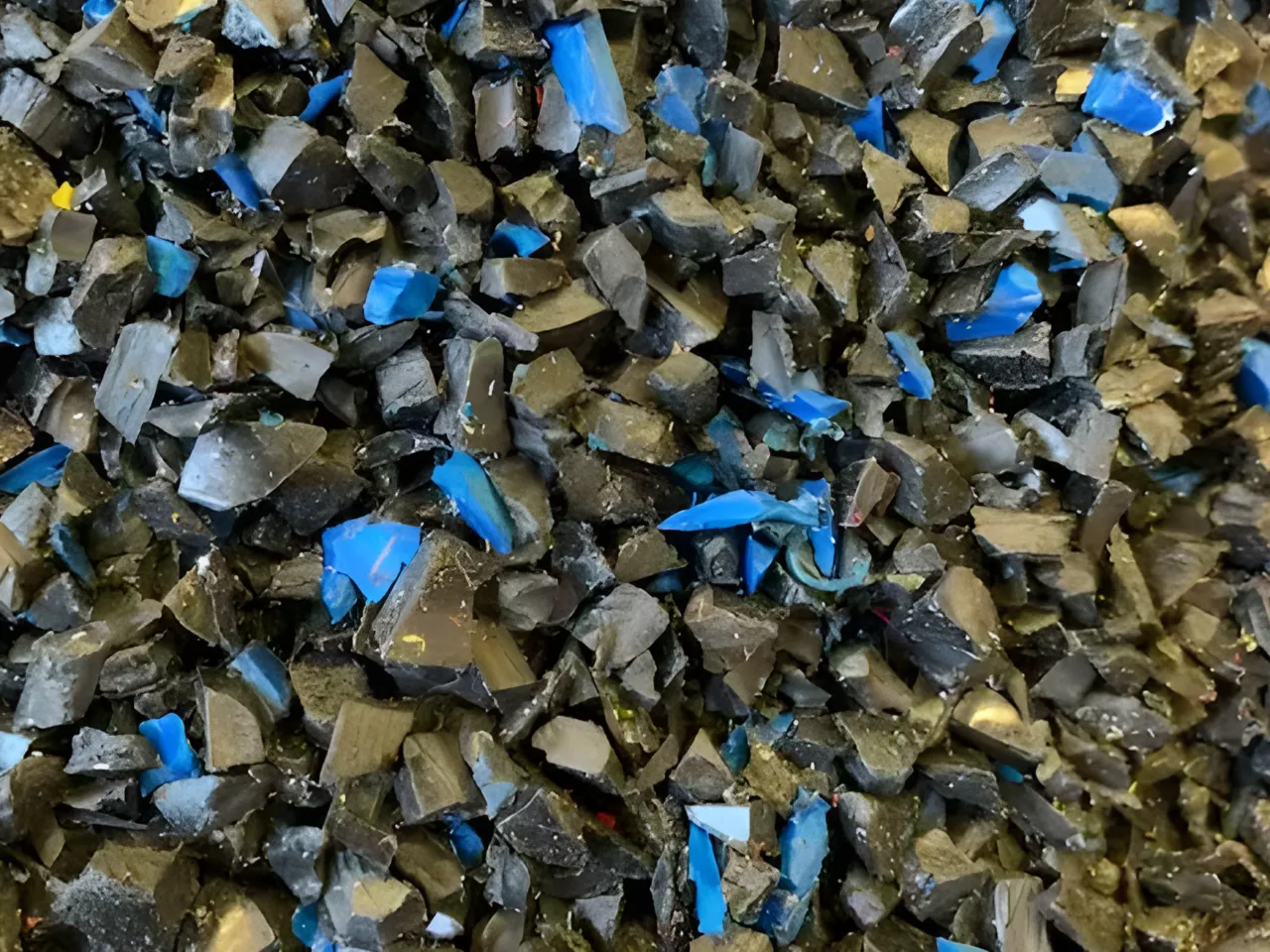
PVC regrind
PVC regrind is widely used in pipes, flooring, cable insulation, and window frames due to its durability, chemical resistance, and adaptability for various applications.
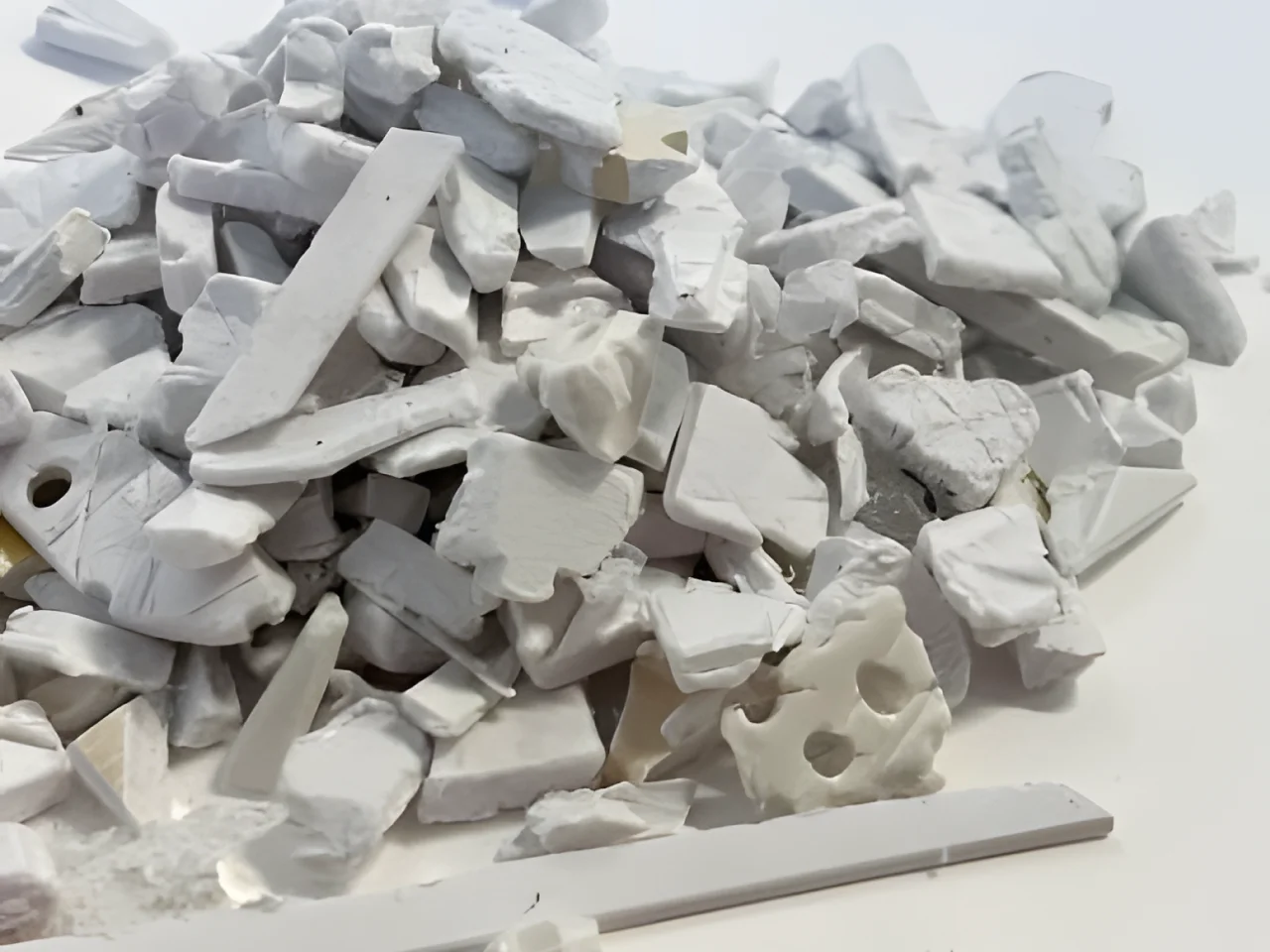
ABS regrind
ABS regrind is commonly used in automotive parts, electronics housings, toys, and appliances, valued for its toughness, impact resistance, and excellent surface finish.
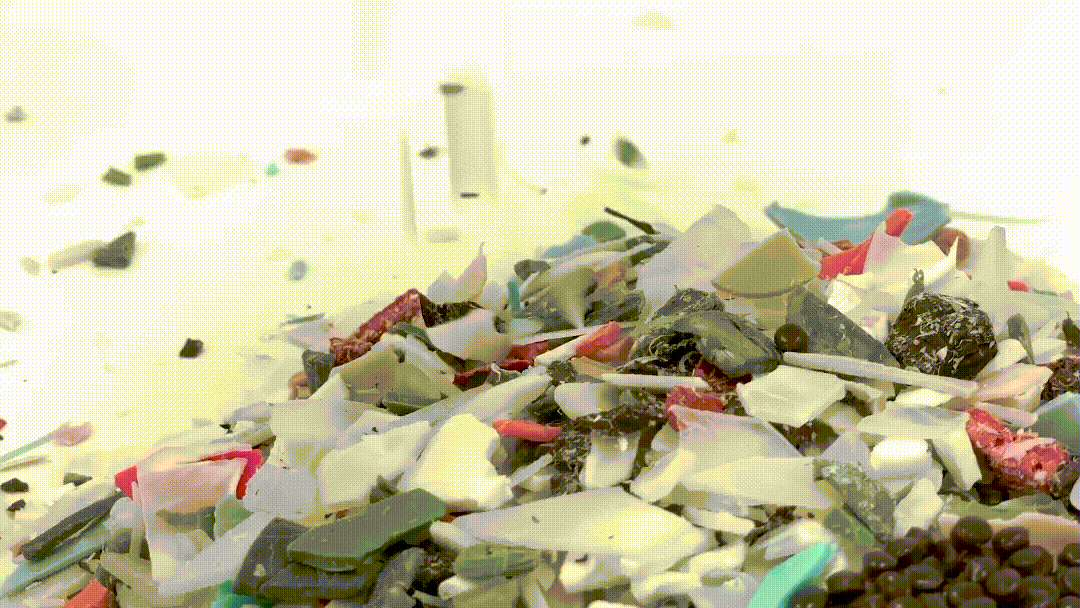
Rigid Plastic
Producers are exploring solutions for PE pipes, PP containers, ABS automobile components, and more, and the origins of these wastes are diverse across industries.
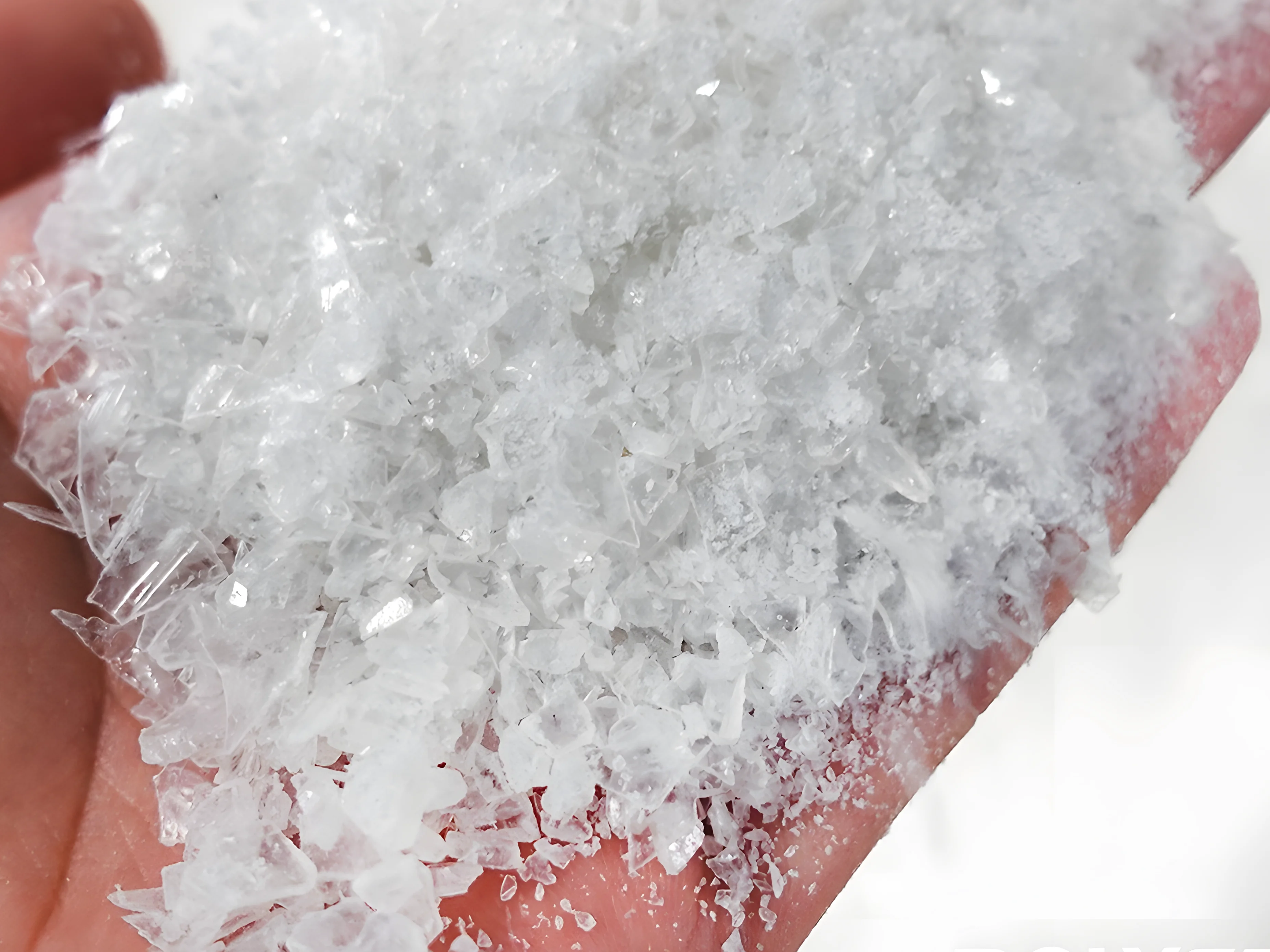
PET regrind
PET regrind is extensively used in bottles, food containers, and packaging materials due to its strength, clarity, and excellent barrier properties, making it ideal for preserving freshness.
Our Process
Pre-washing and Sorting
The first step involves removing large contaminants and prepping materials for further processing.
Granulator
Material is reduced to smaller pieces, allowing for more efficient cleaning and processing.
Intensive Washing
A thorough cleaning process removes any remaining labels, dirt, and adhesives.
Separation
Contaminants and non-target materials are separated, leaving only the desired materials.
Rinsing and Dewatering
Final cleaning and moisture removal to ensure the material is ready for further use.
Drying
Thermal drying is used to achieve optimal moisture content for the final material.
Key Components
Screw Feeder Specifications
The Screw Feeder is designed for durability and efficiency in material handling processes.
- Material: 304 stainless steel
- Shell & Blade Thickness: 3mm
- Screen Hole Thickness: 2mm
- Spiral Diameter: Customized based on output size
Primary Functions:
- Conveying materials
- Filtering water
- Cleaning surface sediment from materials
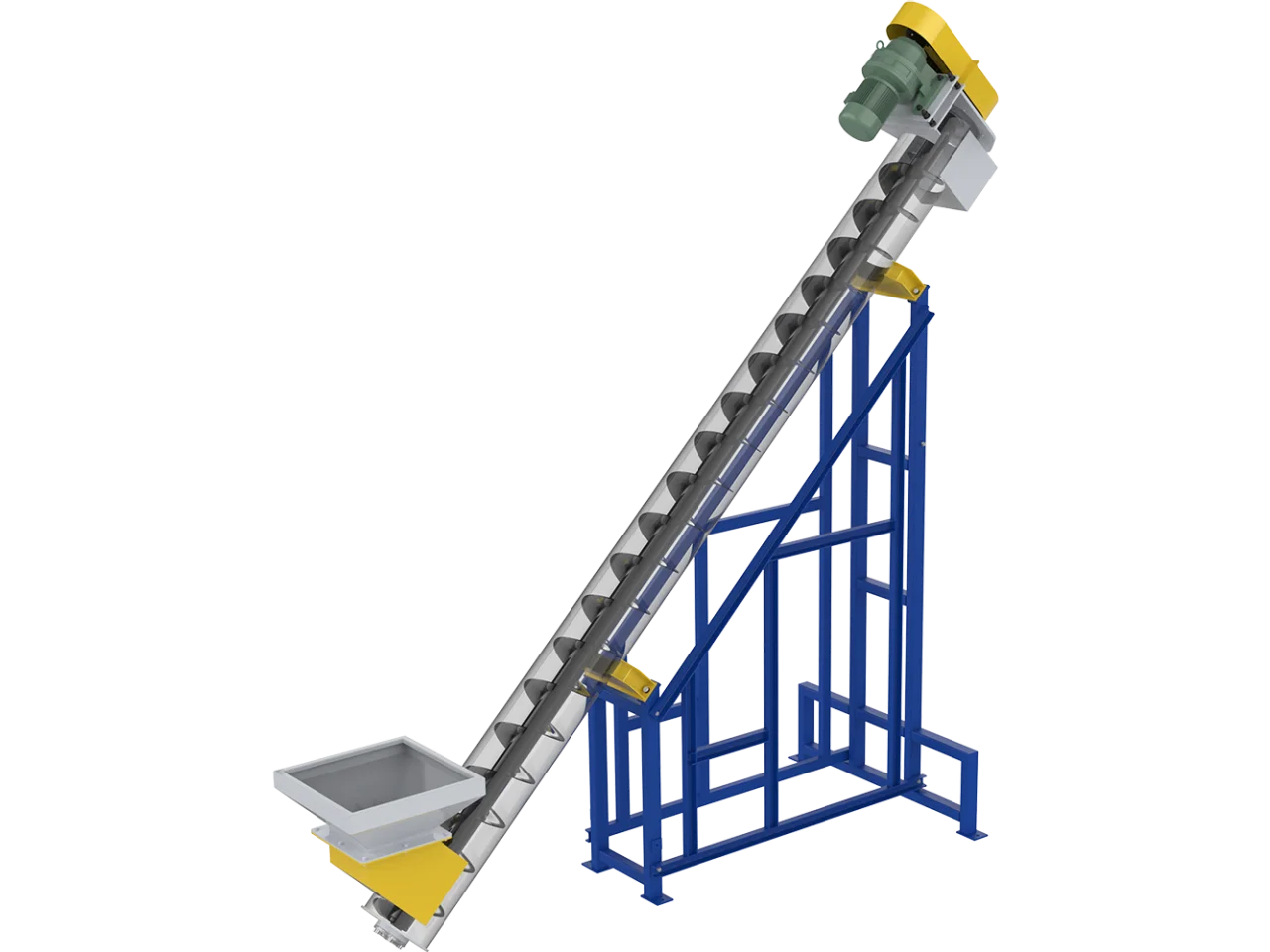
Wet Plastic Granulator Specifications
The Wet Plastic Granulator is an upgraded version of our general-purpose granulators, designed for efficient cutting and pre-cleaning of plastic bottles, films, and rigid materials.
- Rotor Speed: 400-600 RPM
- Blade Material: D2 high-carbon, high-chromium steel
- Cutting Arrangements: V-shape or double-scissor cut
- Screen Filter Size: 10mm – 100mm (customizable)
Primary Functions:
- Cutting plastic materials
- Pre-cleaning and loosening contaminants
- Reducing dust buildup in recycling plants
- Extending blade and machine durability
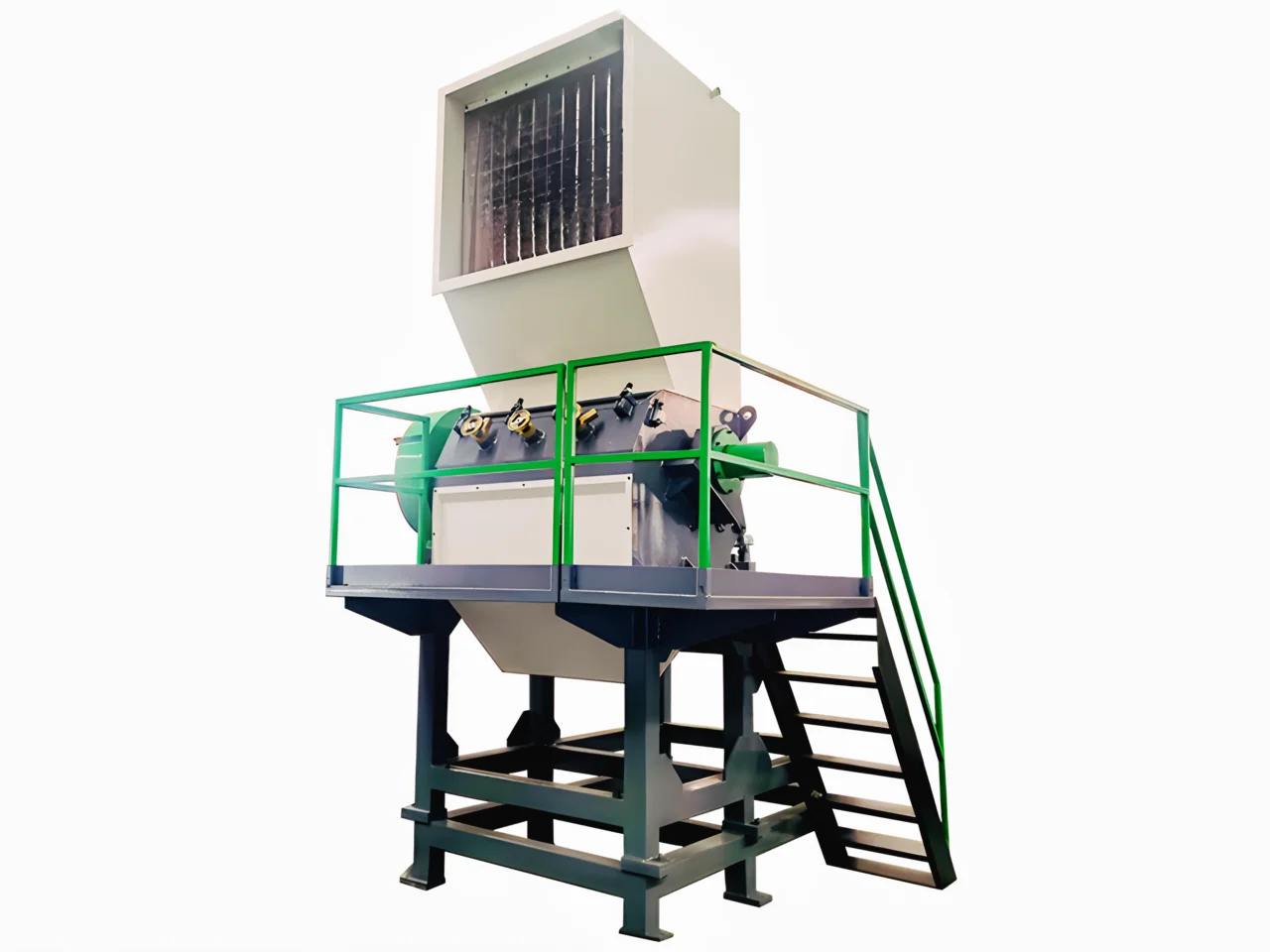
Friction Washer Specifications
The Friction Washer is designed for efficient cleaning and transportation of plastic flakes, films, and regrind materials.
- Rotor Speed: 500-600 RPM
- Water System: Top inlet, bottom outlet
- Operation: Continuous
- Cleaning Method: Friction-based
Primary Functions:
- Cleaning plastic materials
- Transporting materials between machinery
- Removing soil, sand, and other contaminants
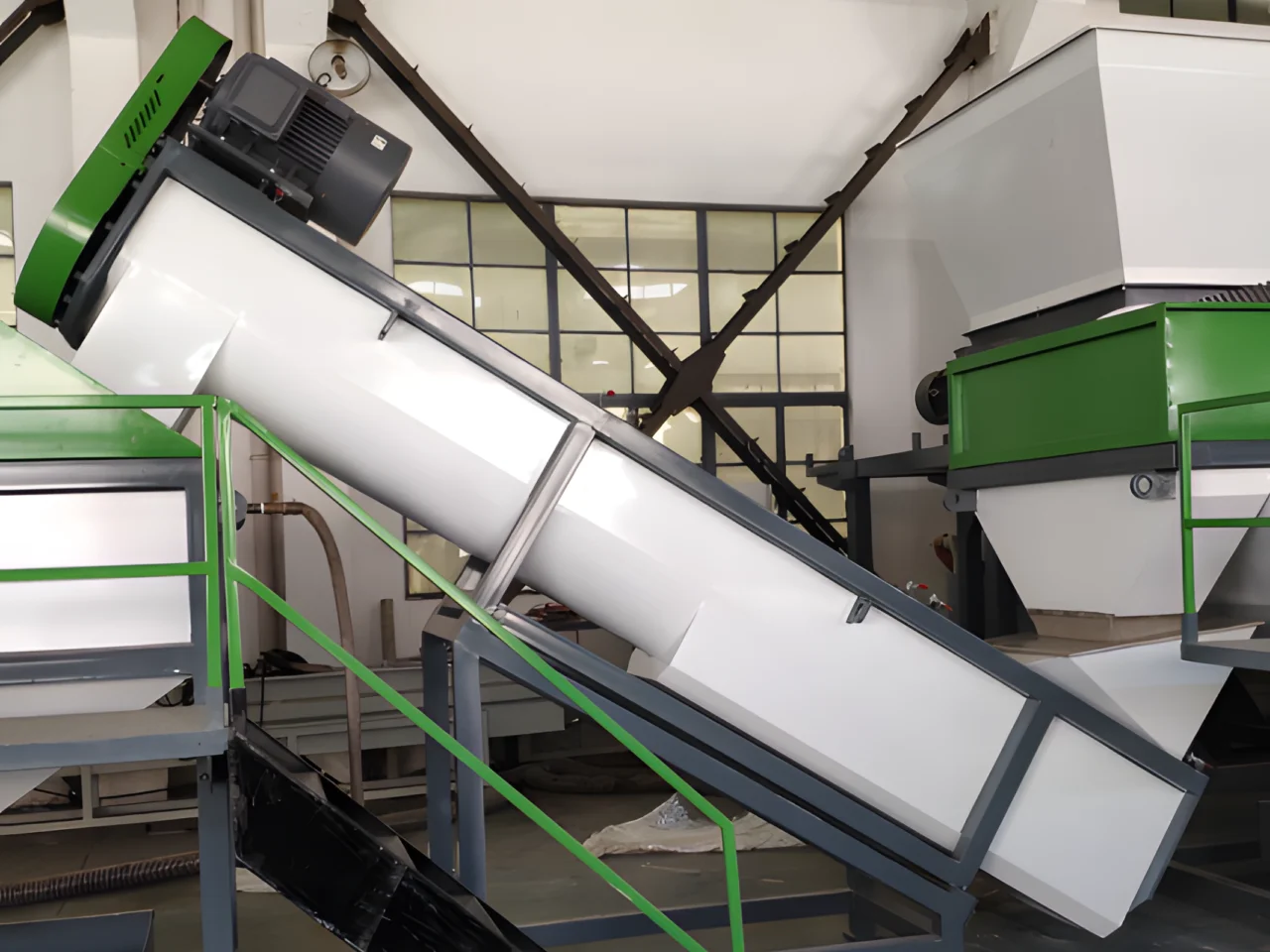
Floating Separation Tank Specifications
Our Floating Separation Tank is designed to efficiently segregate PP and PE plastics from co-mingled streams while simultaneously cleaning the materials for further processing.
- Interior Width: 1000mm – 1800mm
- Total Length: 4 – 7 meters
- Interior Material: Type 304 Stainless Steel
- Exterior Frame: Carbon Steel
- Paddle Motors: 1.5KW*2 (frequency control)
Key Features:
- “W” shaped bottom for improved efficiency
- Dual-section design for better contamination management
- Water-based separation for PP and PE plastics
- Simultaneous cleaning and separation
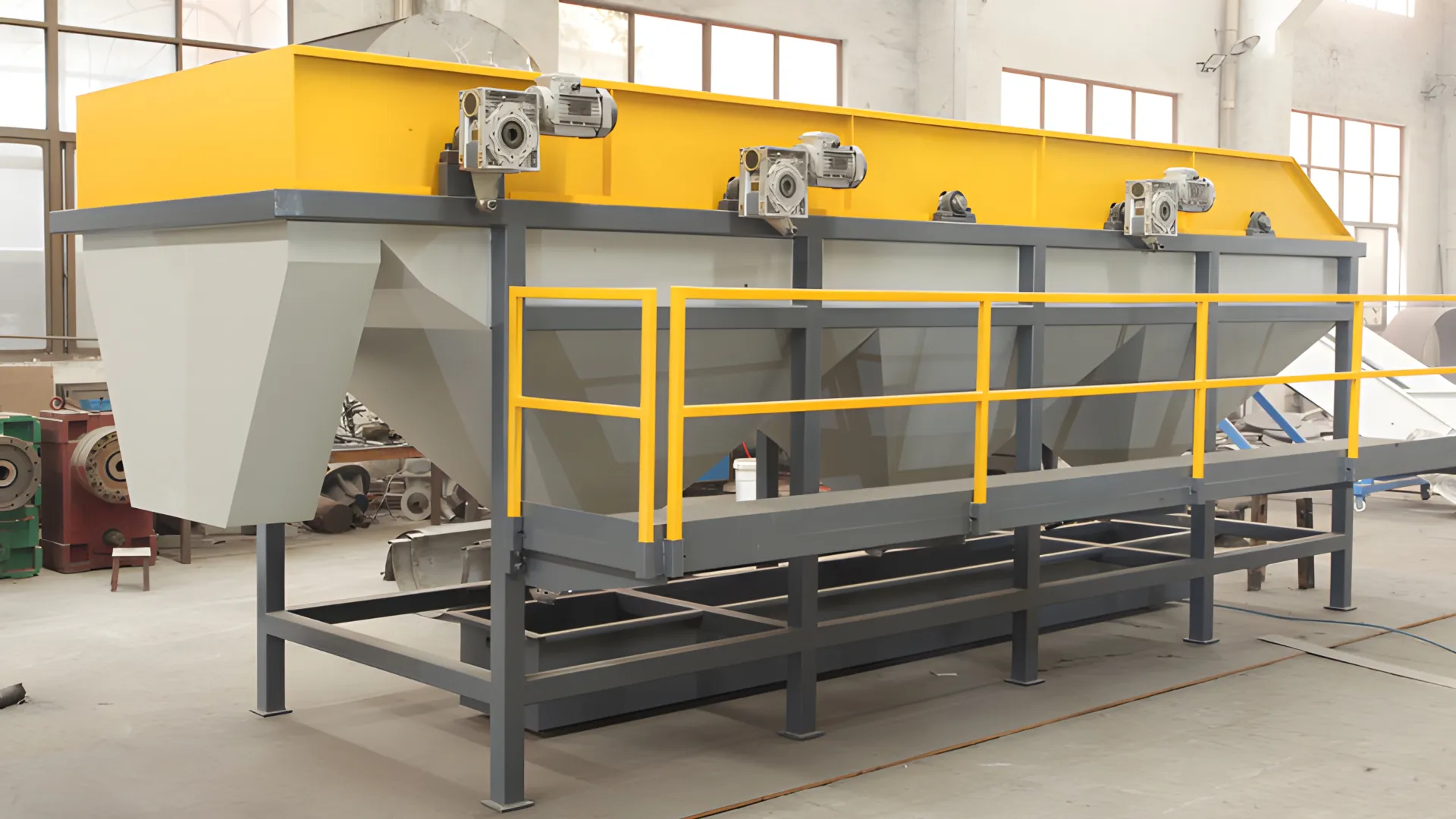
Hot Washer Specifications
Our advanced continuous Hot Washer system offers unparalleled efficiency and cleaning abilities for PET flakes, HDPE flakes, and other plastic regrinds. It’s designed for continuous operation and is extremely effective at removing oils and other stubborn contaminants in a single wash cycle.
- Operation Mode: Continuous
- Washing Method: Hot chemical bath
- Internal Mechanism: High-speed rotary paddles
- Suitable Materials: PET flakes, HDPE flakes, other plastic regrinds
Key Features:
- Continuous operation for higher efficiency
- Effective removal of oils and stubborn contaminants
- Single wash cycle for most applications
- Friction-based cleaning for thorough results
- Can be combined with cold washing system for enhanced results
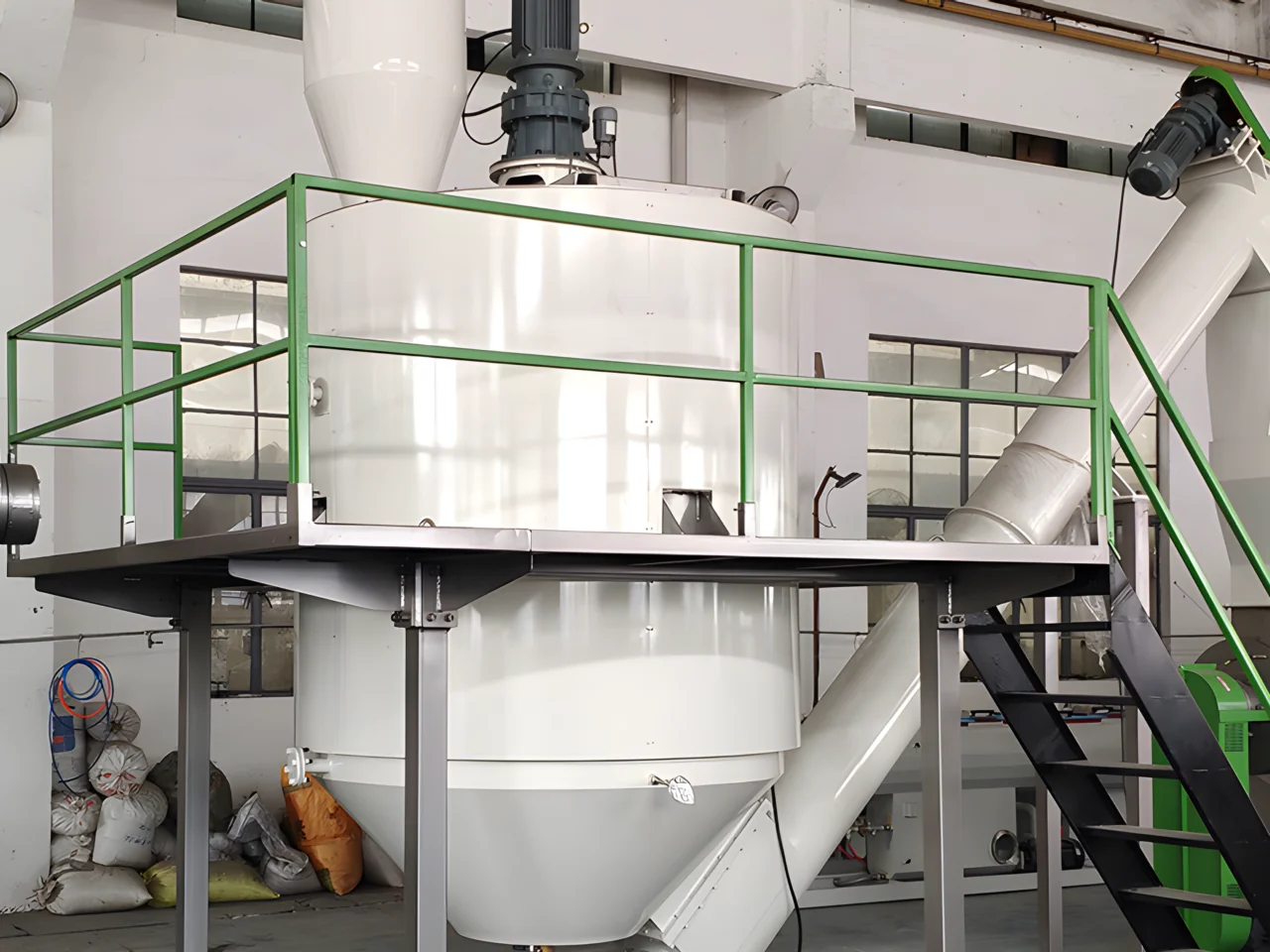
Centrifugal Dryer Dewatering Specifications
Our Centrifugal Dryer Dewatering machine is a highly efficient, low energy consuming equipment designed to partially remove water from plastic materials using centrifugal force. It’s an essential first step in PE film and PET bottle washing lines.
- Rotation Speed: Approximately 1,000 RPM
- Moisture Reduction: To approximately 20-30%
- Main Components: Long shaft with paddles, mesh screen tunnel
- Casing: Metal container with external electric motor
Key Features:
- High efficiency with low energy consumption
- Handles material with high water content
- Suitable for PET flakes, PP/PE flakes, and other plastic regrinds
- Patented design doubles as a friction washer for cooling and cleaning
- Water recycling capability
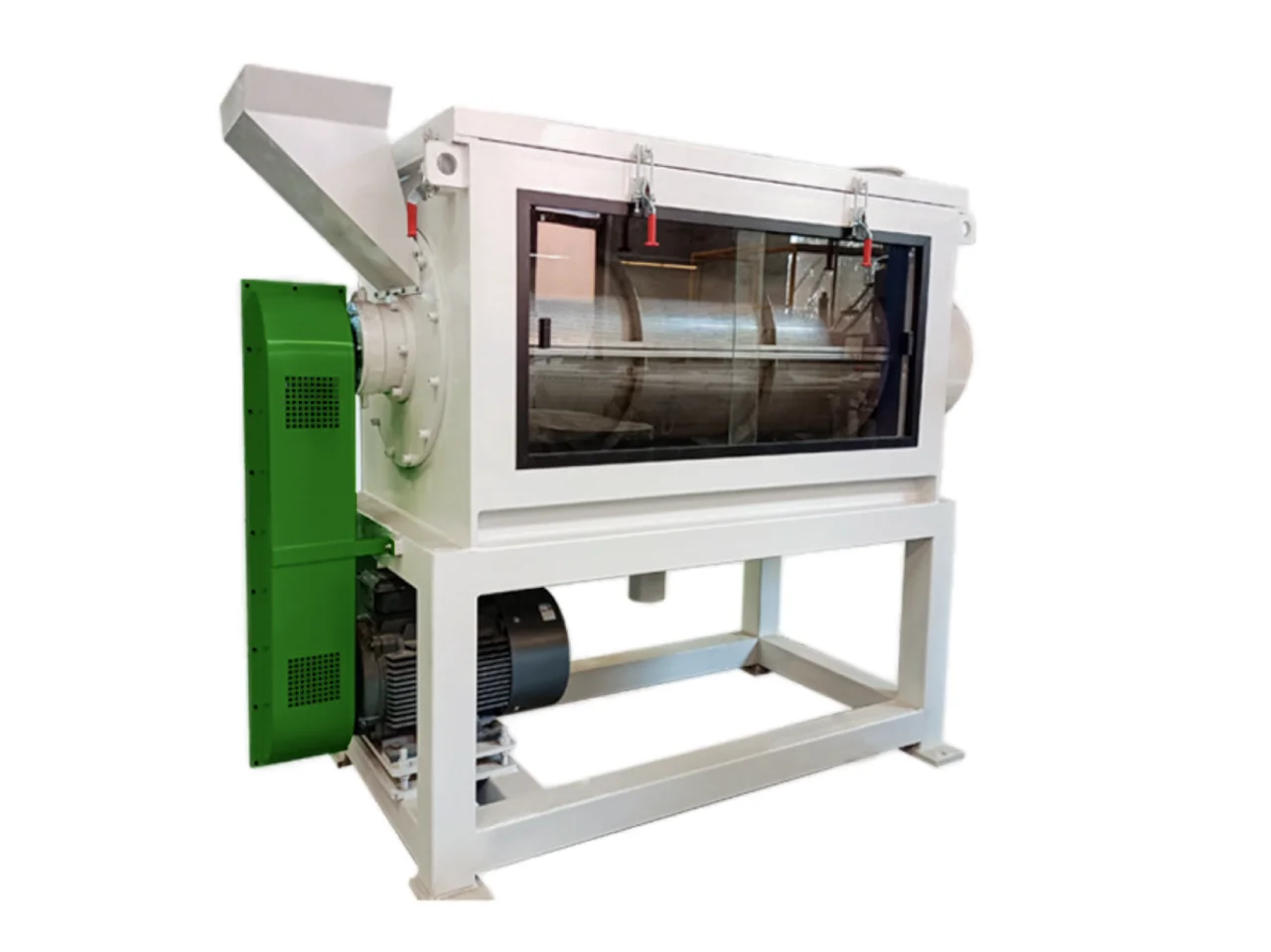
Thermal Dryer Specifications
Our Thermal Dryer is designed for efficient moisture removal through dehydration, ideal for plastic film and PET washing lines. It’s an essential final step in reducing moisture levels to below 3%.
- Model: RSJ800
- Blower Power: 5.5 KW
- Heating Power: 36 KW
- Pipe Diameter: ⌀159mm
- Pipe Material: Type 304 Stainless Steel
Key Features:
- Continuous drying process
- Integrated cyclone separator
- Hot air dehydration system
- Efficient dust and fines removal
- Scalable design (can use multiple units in series)
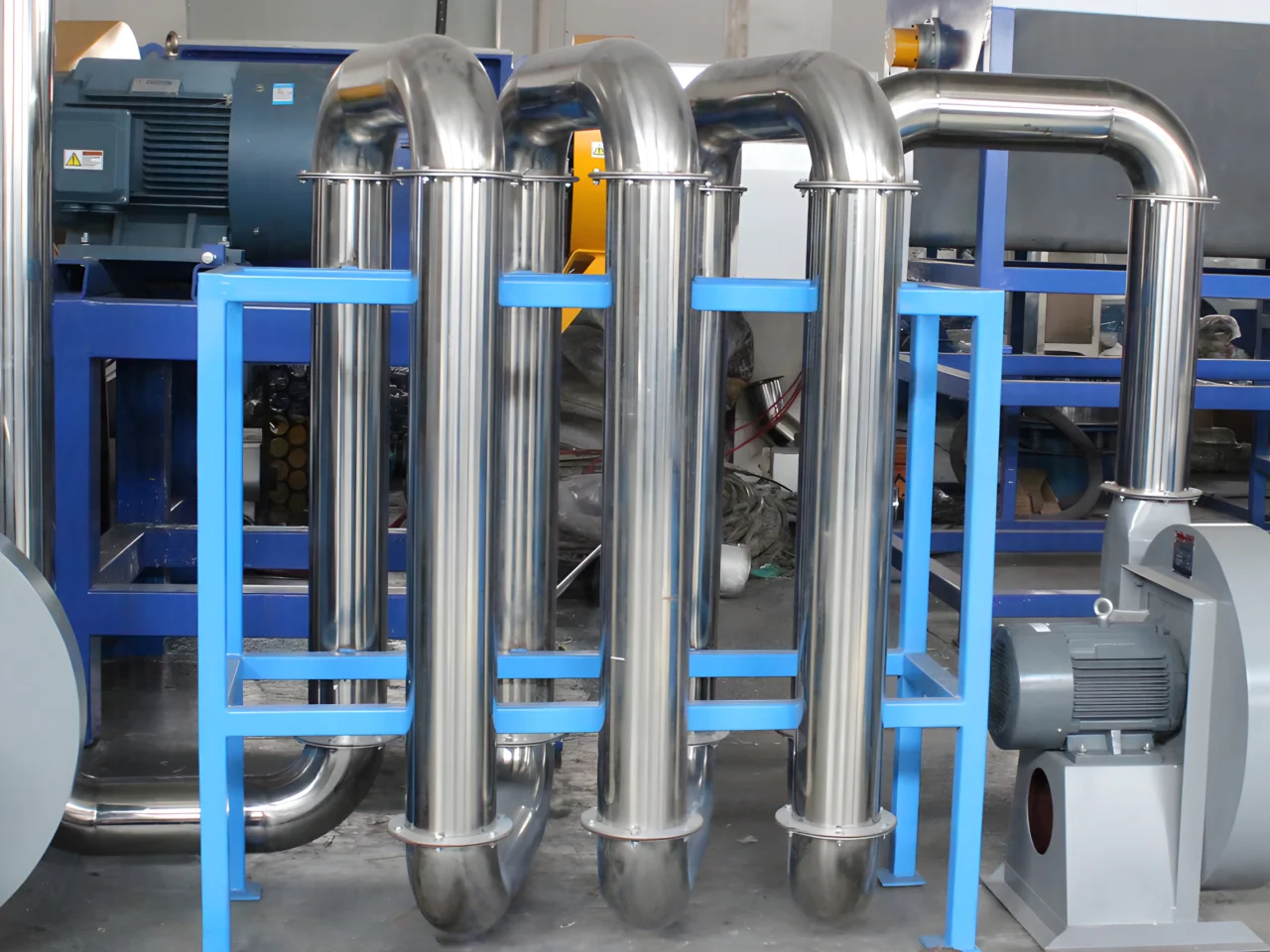
Zig-Zag Air Classifier Specifications
Our unique Zig-Zag Air Classifier is designed to separate lightweight contaminants from heavier plastics, making it an essential component in PET bottle recycling lines. It also serves as an effective partial drying solution for the material stream.
- Separation Medium: Air
- Sorting Method: Weight-based separation
- Primary Application: PET bottle recycling
- Contaminants Removed: Paper labels, plastic labels, and other lightweight materials
Key Features:
- Efficient separation of lightweight contaminants
- Partial drying of material stream
- Versatile application in weight-based material separation
- Unique zig-zag design for enhanced separation
- Dual-exit system for separated materials
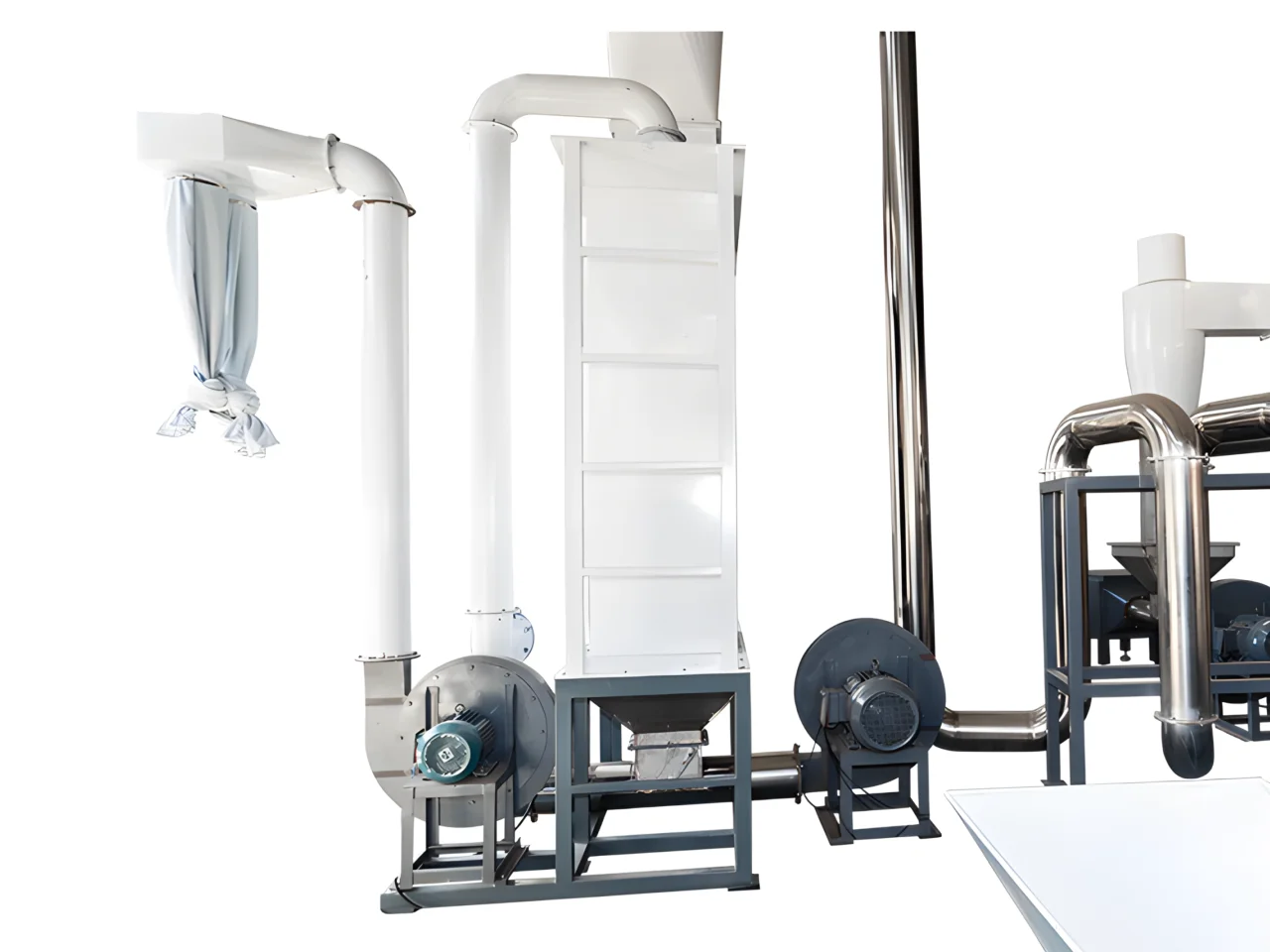
Our Technology Advantage
Eco-Friendly
Designed for reduced water and energy consumption, maximizing sustainability.
High Output Quality
Superior cleaning technology produces high-grade recycled materials for premium reuse.
Versatile Application
Engineered to capably process various types of rigid plastics with high efficiency.
Ready to Upgrade?
Contact our team of experts today for a customized solution and discover how you can enhance your plastic recycling capabilities.
Get a QuoteFrequently Asked Questions
1. What is the main purpose of a rigid plastic washing line?
The primary purpose is to take highly contaminated rigid plastic waste (like used drums, pipes, crates, or car bumpers) and transform it into clean, dry, high-quality plastic flakes. These flakes are then ready to be used in a pelletizing/granulating machine to produce new plastic pellets.
2. What types of rigid plastics can this line recycle?
This washing line is specifically designed for polyolefin plastics. It is highly effective for PP (polypropylene) and HDPE (high-density polyethylene). It can also process other rigid plastics such as ABS, PS, and more. It is not suitable for PET bottles, which require a different process.
3. How is this line different from a PET bottle washing line?
The key difference lies in the separation technology. This line uses a float-sink separation tank. PP and HDPE plastics have a density less than water, so they float. Contaminants like PET, stones, and metal sink to the bottom. This method is ineffective for PET bottles, which also sink and require different separation techniques like air classifiers.
4. How clean and dry are the final plastic flakes?
The system is designed to produce exceptionally clean flakes. The multi-stage washing process, including high-speed friction washers and optional hot washers, removes dirt, sand, labels, and glue. The final dewatering and thermal drying stages ensure a final moisture level of less than 1%, which is crucial for high-quality pelletizing.
5. Can this washing line be customized for my specific needs?
Yes, absolutely. Each washing line is custom-built based on your requirements. We consider the type of plastic you're processing, the level and type of contamination, your desired capacity (kg/hr), and your final quality standards to design a solution that is perfect for your operation.
6. What information should I provide to get an accurate quote?
To give you the most accurate quote, please provide us with: 1) The primary type of plastic you will be recycling. 2) The source and type of contamination (e.g., post-consumer crates with labels, industrial pipes with oil). 3) Your required capacity in kg/hr. 4) Any specific requirements for the final product.