Recycling Products
More recycling equipment
Plastic washing and recycling system CAD drawing reference
Different projects, different configurations.
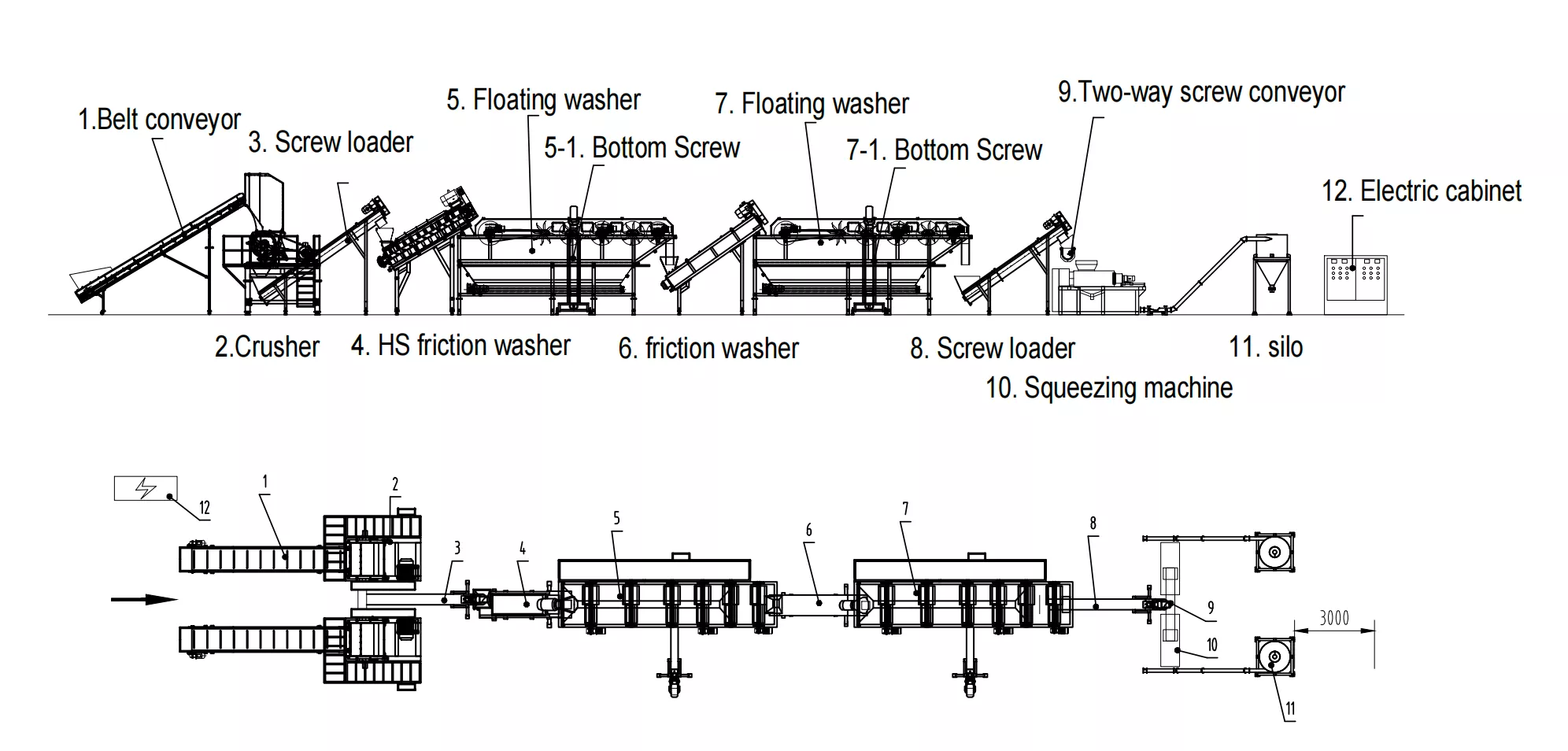
Get Plastic Recycling Machine Solutions
OUR SKILL
Placing An Order Easy
Just Follow The Steps
Whether you require a single plastic recycling machine, a turnkey recycling plant, or a bespoke recycling solution, we guarantee top-tier customer service and communication for efficient order processing and project execution.
Here’s our standard procedure for initiating orders and custom projects:
Plastic Recycling Machine Blogs
Insights and Updates on Recycling Technology
Stay informed with our latest blog posts covering a wide range of topics in the plastic recycling industry. From innovative machine designs to best practices in recycling processes, our blogs offer valuable insights for both industry professionals and environmental enthusiasts.
1200+ happy client
WHAT SAY
Latest From Media
Stay Informed with Our Device Videos
Explore our collection of informative videos showcasing our latest plastic recycling machines in action. From product demonstrations to maintenance tips, our media section keeps you updated on the cutting-edge technology in plastic recycling.
Frequently Asked Questions
Get answers to the most common questions about our Plastic Recycling Machines and how they can benefit your operations.
We’re dedicated to delivering top-tier recycling machinery that combines efficiency, durability, and value. We understand the significant investment involved in purchasing recycling equipment, which is why we’re committed to excellence in every aspect. We invite you to visit our factory and experience our commitment firsthand.

How much do your recycling machinery cost?
To provide you with the most accurate and fair pricing, we customize each quote based on specific needs, shipping rates, and local requirements. Please contact us directly for a detailed quotation.

- Standard machines: Approximately 30-45 days post-contract.
- Plastic Recycling&Washing lines: Between 60 to 90 days.
- Custom projects: Timeline specified in the contract.

Our ordering process is straightforward. Contact us with your equipment needs and any custom specifications. Discover more about our ordering process and how we can assist you in making the best choices.

Yes, we highly encourage testing. For complete systems, we perform a comprehensive trial run before shipment. We invite you to participate in this crucial phase to ensure the machinery meets your standards.

offers a comprehensive one-year warranty on all machines and parts, ensuring they are free from defects.

Yes, we provide a full installation package.
Our certified engineers will assist with the setup and commissioning of your machinery. the client is responsible for arranging and covering travel and accommodations for our engineers. Installation duration varies by project size, typically requiring 7-14 days.