Turnkey Solutions for Immaculate Plastic Flakes
We design and build complete, custom-tailored plastic washing lines that transform contaminated post-consumer or post-industrial waste into high-purity, high-value recycled flakes, ready for profitable reuse.
Get a Custom Proposal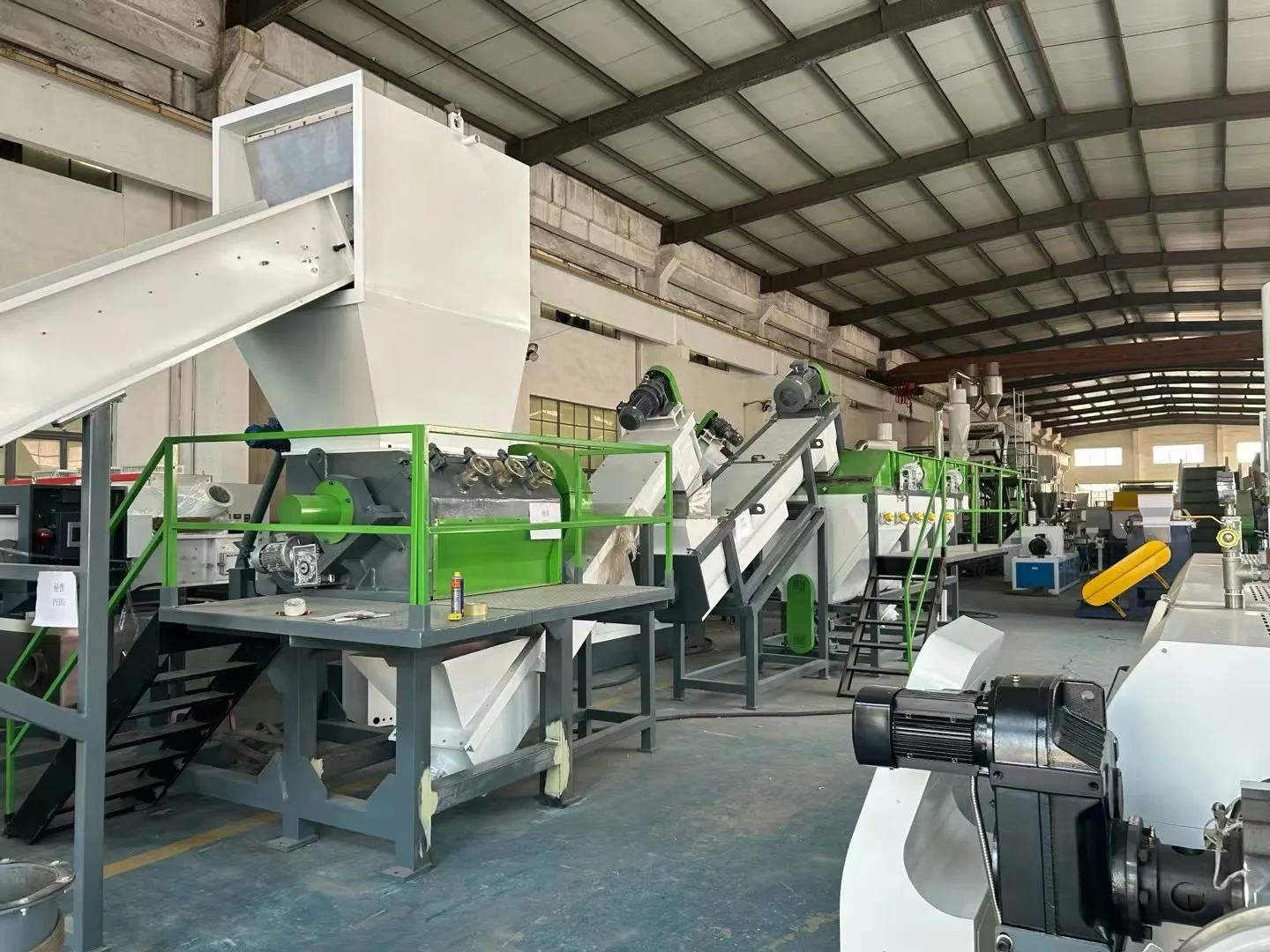
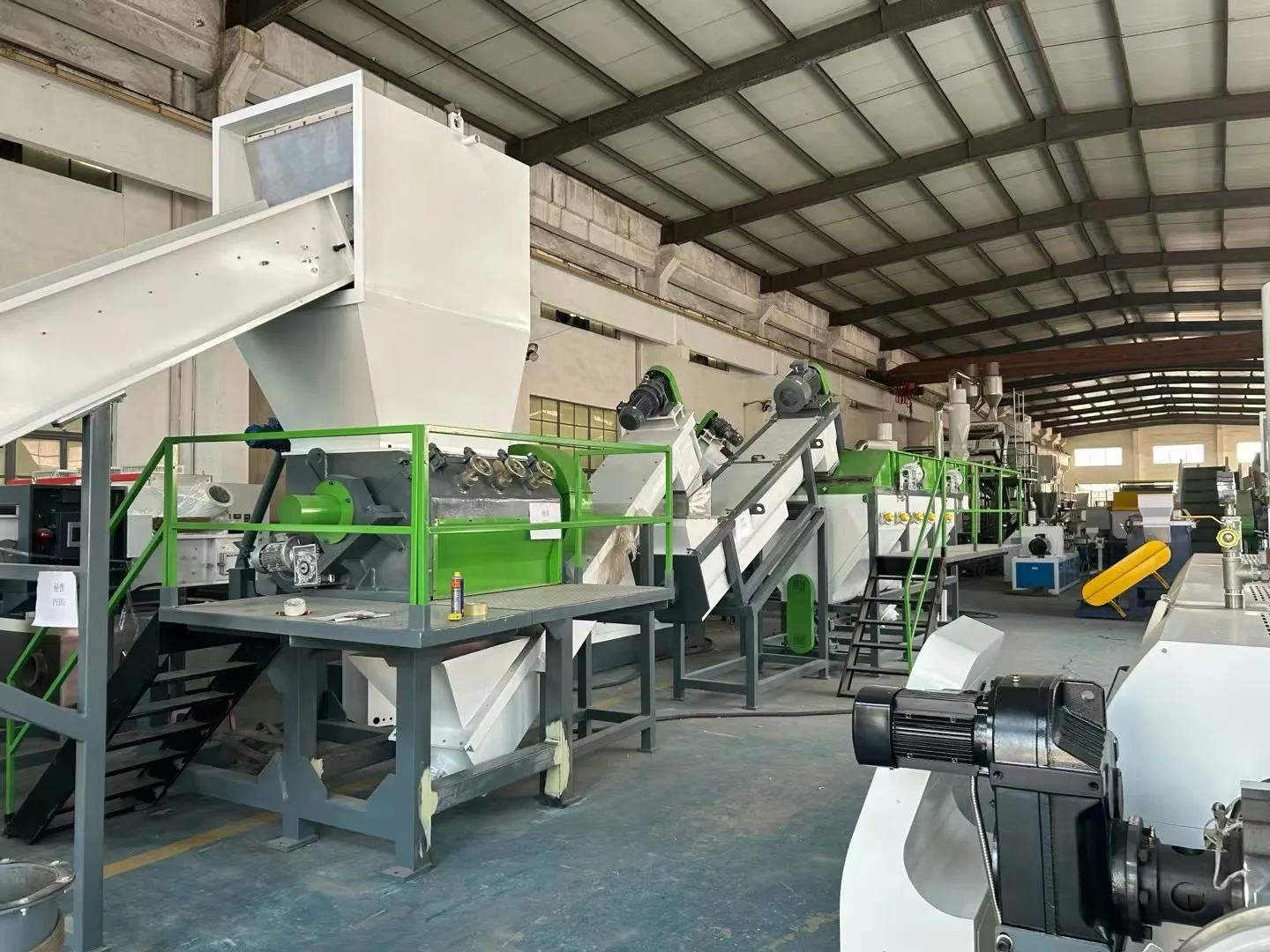
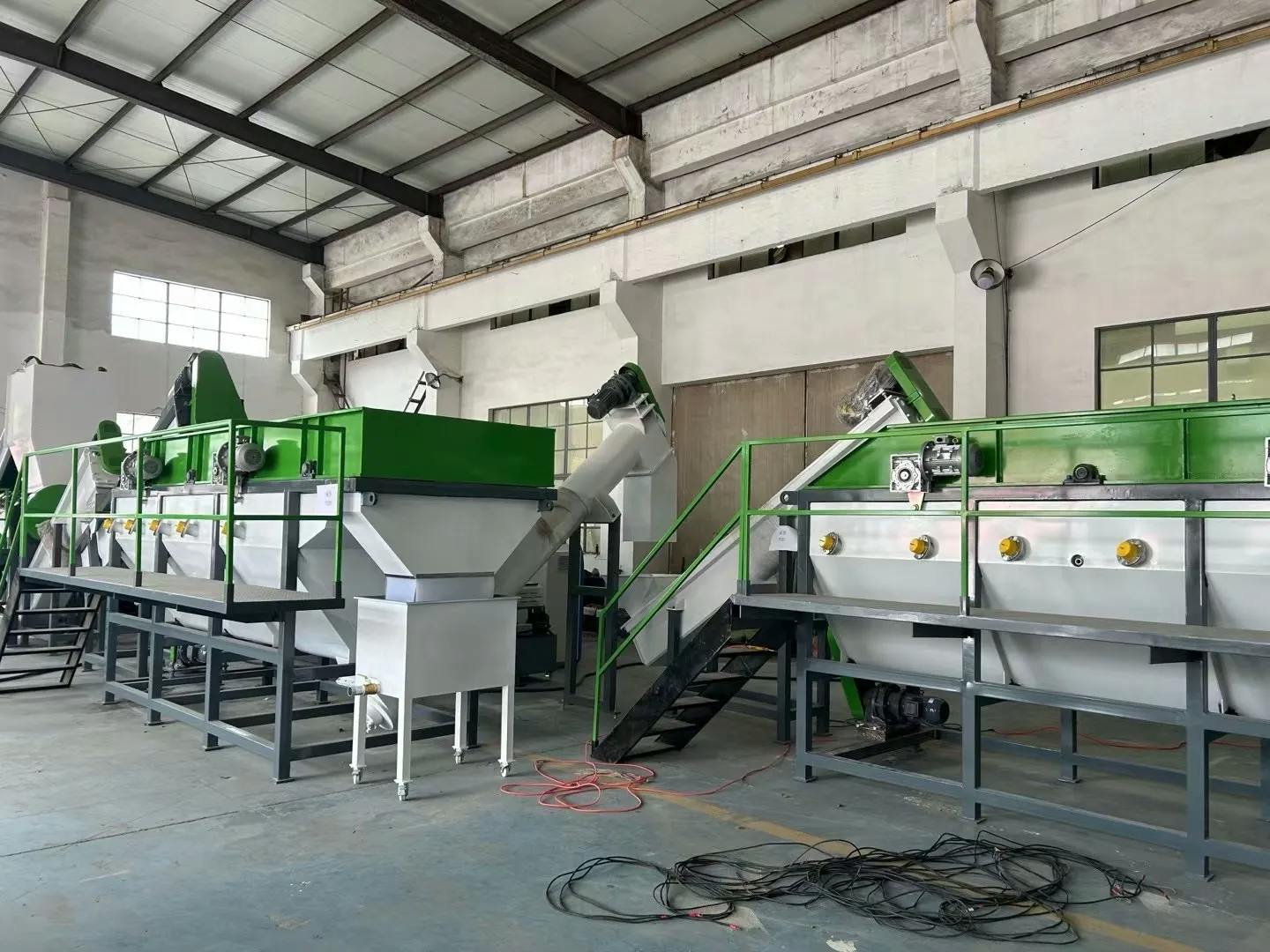

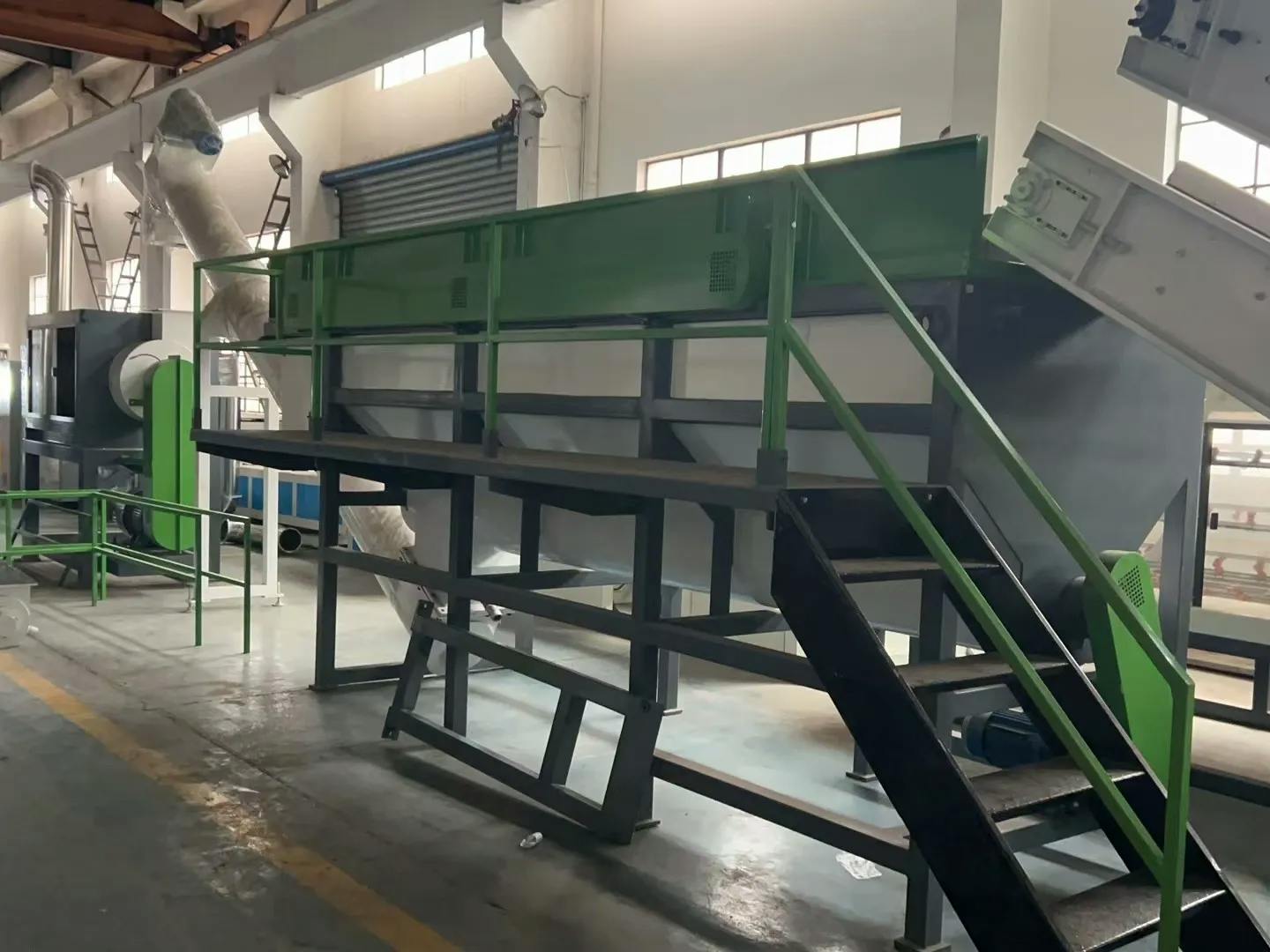
Your Partner for High-Quality Recycling
We don’t just sell machines; we deliver comprehensive, reliable solutions engineered for your specific needs and long-term success.
Fully Custom Solutions
Every line is designed around your input material, capacity requirements, and purity targets, ensuring optimal performance and efficiency.
Unmatched Output Purity
Our multi-stage washing, rinsing, and separation processes remove even the toughest contaminants, delivering market-ready flakes.
End-to-End Support
From initial design and installation to training and after-sales service, our team provides expert support throughout the project lifecycle.
See Our System in Action
Watch a complete walkthrough of one of our advanced PET bottle washing lines, demonstrating the process from raw material to clean, finished flakes.
Our Proven 4-Stage Washing Process
Each stage is meticulously engineered to work in harmony, progressively cleaning and purifying the material for a superior final product.
Size Reduction & Pre-Washing
Baled or loose material is shredded or granulated. This initial stage often includes dry pre-cleaning to remove loose dirt and fines.
Intensive Washing & Separation
Flakes undergo high-speed friction washing and pass through floating sink tanks to separate plastics by density (e.g., PET from PP/PE caps).
Hot/Cold Rinsing
Multiple rinsing stages, including optional hot washing, remove residual glues, oils, and chemical contaminants for the highest purity.
Drying & Fines Removal
A centrifugal dewatering machine and thermal dryer reduce moisture below 1%. A zig-zag classifier removes any remaining dust or labels.
Typical System Specifications
We offer a range of standard capacities, and all systems can be fully customized. The following are examples for a PET bottle washing line.
Parameter | 500 kg/h Line | 1000 kg/h Line | 2000 kg/h Line |
---|---|---|---|
Applicable Materials | PET Bottles, HDPE/PP Bottles, Hard Plastics | ||
Final Product Moisture | < 1% | ||
Final Impurity Content | < 100 ppm | ||
Total Installed Power | ~150 kW | ~280 kW | ~450 kW |
Water Consumption | ~5ton/hr | ~8ton/hr | ~12ton/hr |
Frequently Asked Questions
Absolutely. We design specific washing lines for soft plastics like agricultural film or post-consumer LDPE film. These systems use specialized friction washers and dewatering presses optimized for flexible materials.
Our lines are designed for water efficiency, typically consuming 1-2 tons of fresh water per ton of plastic. We also offer integrated water treatment and circulation systems that can recycle up to 80% of the process water, significantly reducing your operational costs and environmental footprint.
The footprint depends on the capacity and components. A standard 1000 kg/h PET bottle washing line typically requires an area of approximately 500-600 square meters (e.g., 60m long x 10m wide). We provide detailed layout drawings during the proposal stage.
Ready to Produce High-Quality Recycled Plastic?
Contact our engineering team today for a free consultation and a detailed proposal for a washing line built to your exact specifications.
Request a Free Quote