The entire line is designed to clean shredded PP/PE regrind, featuring a friction washer, floatation tank, centrifugal dryer, squeezer, extruders, and pellet cutting system. Below are explanations for some of the key machines:
Working Principle
The high-speed friction washer is a suggested but not mandatory piece of equipment in a plastic film washing line. At the heart of a friction washer is a lengthy, rapidly-rotating shaft fitted with numerous angled panels or paddles. Surrounding this rotating shaft is a mesh screen tunnel used for dewatering. These are then enclosed within a rectangular box where water jets and nozzles are mounted and aimed at the mesh screen.
The sink float tank serves two functions:
- Cleans: The plastic film is allowed to soak in a large tank of water, loosening debris.
- Separation: The loosened debris and heavier contaminants will sink while the plastic films float. The top layer continues to the next stage in the washing line, while the sunken particles are removed.
The final stage of a plastic film washing line is the drying process. The wet plastic films need to be dried before being extruded into plastic granules, the final step in the plastic film recycling process. During extrusion, plastic films are melted into a continuous stream of molten polyethylene plastic, squeezed through a die (similar to how spaghetti is made), and then cut into pellets or granules. If the plastic films are not adequately dried before extrusion, the moisture becomes trapped within the molten plastic, creating air bubbles in the final granules.
Here, we use a squeezer to mechanically compress and heat the material. The material from the squeezer is densified. The resulting film is generally dry enough for extrusion, with approximately 3% moisture.
This provides a clearer understanding of typical machinery used in a standard plastic film regrind washing line. There is no single correct way to set up a film washing plant; however, careful consideration should be given based on the type of plastic film being recycled and the type and level of contamination present. We are pleased to custom-build the line for you.
Technical Specifications
Input Capacity | Size | Operator | Installation Power |
---|---|---|---|
500kg/hr | 45m*15m*6m | 3-4 | 499KW |
1000kg/hr | 50m*15m*6m | 3-5 | 599KW |
- CE certification available.
- Larger, more powerful models available upon request.
Additional Images
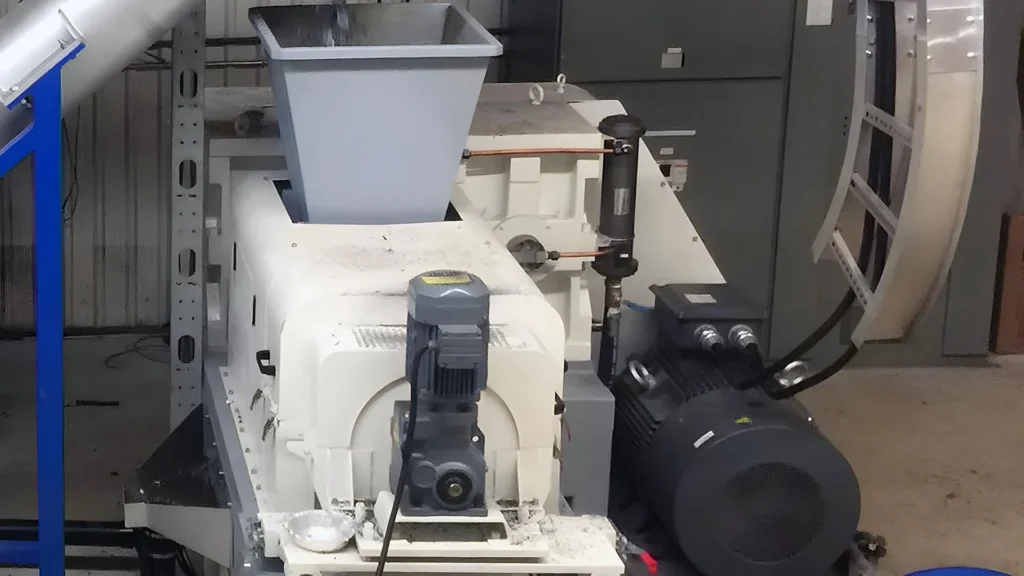
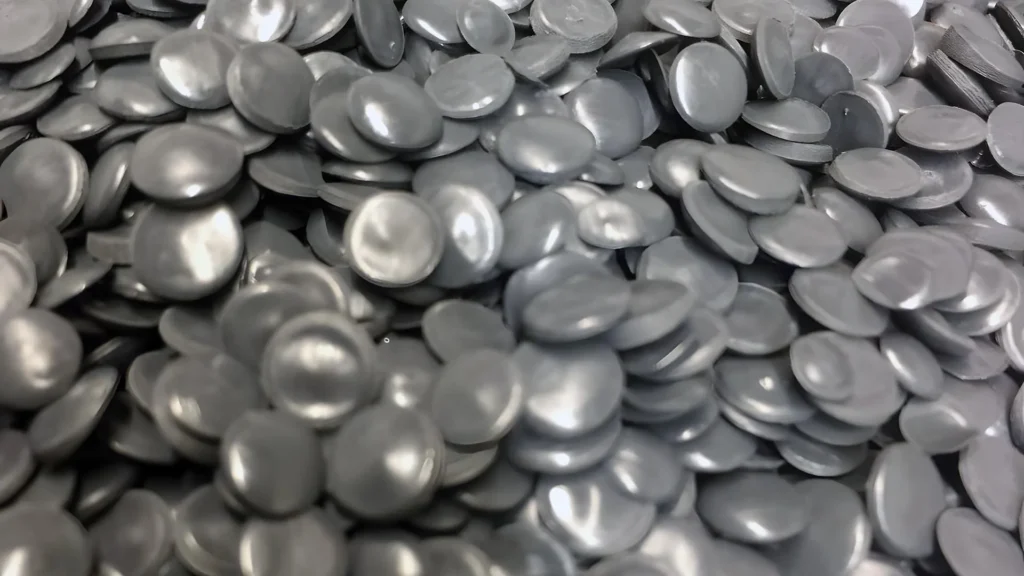
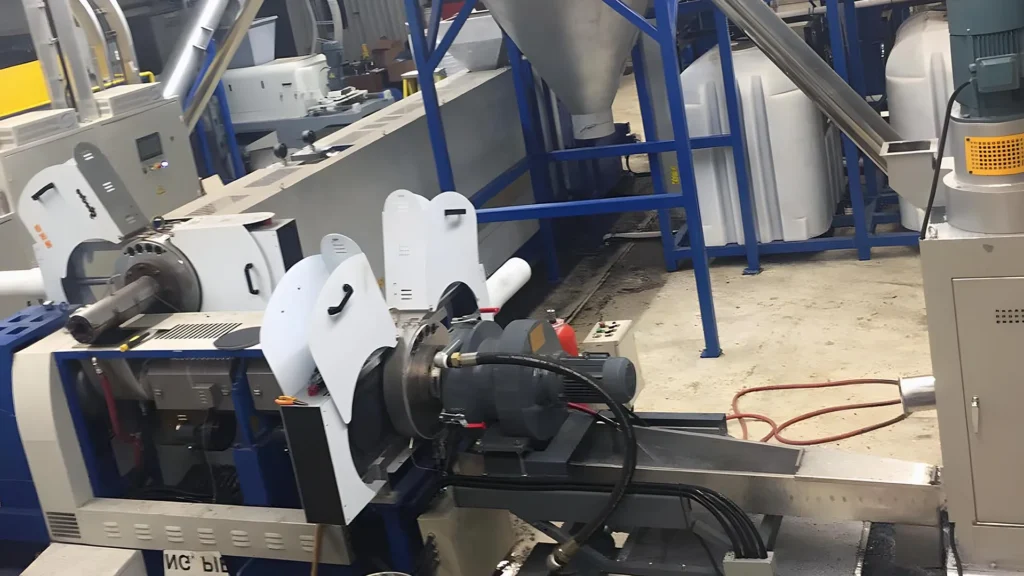
Warranty & Installation
All recycling machinery comes with a 1-year limited warranty.
We offer installation packages where our engineers travel to your facility to guide you through the installation process. Routine maintenance teams and operations consultants can also be arranged to ensure your recycling plant runs smoothly year after year.
Inquire Now
To get the latest prices and lead times, send us a message using the form below.
Comments are closed.