Introduction: The 2025 Imperative for Advanced Plastic Recycling
The year 2025 is not just another date on the calendar; it represents a critical turning point for the global manufacturing and recycling industries. Driven by stringent regulations like the EU’s Green Deal, heightened consumer demand for sustainability, and ambitious corporate ESG (Environmental, Social, and Governance) targets, the pressure to effectively manage plastic waste has never been greater. For businesses in Europe and the USA, simply participating in recycling is no longer enough. The new benchmark is efficiency, purity, and profitability.
The challenge lies in transforming diverse and often contaminated plastic waste streams into high-quality, reusable raw materials. This is not a task for outdated methods or piecemeal equipment. It requires a strategic, integrated approach, underpinned by state-of-the-art technology. As a forward-thinking manufacturer or industrial recycler, your success in 2025 and beyond will hinge on your ability to invest in and implement the right processes and machinery.
This article serves as your comprehensive guide to navigating the complexities of industrial plastic recycling. We will break down the essential steps, explore the critical role of modern equipment, and provide actionable insights to help you build a robust and future-proof recycling operation. At Maszyna do rumu, we believe that a well-engineered system is the cornerstone of sustainable manufacturing, and we are here to share our expertise.
The Evolving Landscape: Key Drivers for Recycling in 2025
Understanding the forces shaping the industry is the first step toward developing a winning strategy.
- Presja regulacyjna: The EU’s Single-Use Plastics Directive and ambitious recycling targets (e.g., 55% of plastic packaging waste recycled by 2030) are creating a legal and financial imperative. In the USA, while federal mandates are less uniform, state-level initiatives and EPA goals are pushing the industry in the same direction.
- Economic Incentives: The price of virgin plastics is volatile and subject to geopolitical factors. High-quality recycled pellets (rPET, rHDPE, etc.) are becoming an increasingly stable and cost-effective alternative, creating a strong market for well-processed materials.
- Corporate Responsibility: Global brands have made public pledges to increase the recycled content in their packaging. To meet these promises, they need a reliable supply of premium recycled plastic, creating a direct demand for output from advanced recycling facilities.
These factors converge to create a clear message: investing in a high-performance maszyna do recyklingu and system is no longer an operational cost, but a strategic investment in market leadership and long-term viability.
The Core Workflow of Industrial Plastic Recycling: A Step-by-Step Guide
Achieving high-purity recycled plastic is a multi-stage process. Each step is crucial, and the efficiency of the entire line depends on the performance and integration of the equipment involved.
Step 1: Sorting and Initial Preparation
While large-scale municipal facilities (MRFs) handle initial sorting, industrial recyclers often receive baled, semi-sorted materials. The goal here is to remove gross contaminants and separate plastics by type and colour. Advanced systems may use Near-Infrared (NIR) technology, but for many operations, the first machine in their own line is for size reduction.
Step 2: Size Reduction – The Foundation of Efficiency
Before plastic can be washed or processed, it must be broken down into a uniform, manageable size. This increases the surface area for effective cleaning and ensures consistent feeding into subsequent machines.
- Niszczarki przemysłowe: These are the heavy-duty workhorses for the initial breakdown. A single-shaft or double-shaft shredder is ideal for processing bulky items like purgings, bales of film, or large moulded parts. A robust shredder, such as those in the Maszyna do rumu SR series, can handle high volumes and tough materials, protecting downstream equipment from damage.
- Granulators/Crushers: After shredding, or for smaller, more rigid items, a granulator is used for secondary size reduction. It produces a finer, more uniform “regrind” or “flake.” The design of the cutting chamber, rotor, and screen size are critical for achieving the desired particle size without creating excessive dust.
The choice between a shredder and a granulator—or using both in a two-stage process—depends entirely on your input material.
Step 3: High-Intensity Washing and Separation
This is arguably the most critical stage for determining the final value of your recycled material. Contaminants like paper labels, glue, dirt, food residue, and other non-target plastics must be meticulously removed. A comprehensive washing line is not a single machine, but an integrated system.
- Podkładka cierna: Uses high-speed paddles and water to scrub the surface of the plastic flakes, mechanically removing dirt and labels.
- Float-Sink Tank: A simple yet effective method based on density. It separates polyolefins (PP, PE), which float, from heavier plastics like PET and PVC, which sink. It also allows sand, glass, and metal fragments to sink away.
- Hot Washing System: For post-consumer waste, especially PET bottles, hot washing with a caustic soda solution is essential. This effectively dissolves glues and removes stubborn organic matter, resulting in a much higher purity flake.
- Płukanie: Multiple rinsing stages are needed to remove any residual detergents and contaminants.
The efficiency of your washing line directly impacts the quality and market price of your final product. Maszyna do rumu designs modular washing lines that can be configured to the specific contamination level of your input stream.
Step 4: Dewatering and Drying
Before the plastic flakes can be pelletised, their moisture content must be drastically reduced, typically to below 1%. High moisture can cause defects during extrusion.
- Mechanical Dewatering: A high-speed centrifugal dryer spins the water off the flakes, achieving an initial moisture level of around 2-3%.
- Thermal Drying: A hot air thermal drying system then passes the flakes through heated air tunnels, removing the remaining moisture to reach the target level.
An efficient drying process is vital for energy conservation and ensuring the structural integrity of the final pellets.
Step 5: Pelletising (Extrusion and Granulation)
This is the final transformation, turning clean, dry flakes into uniform, easy-to-handle pellets that can be sold directly to manufacturers.
The process involves feeding the flakes into an extruder, which melts and homogenises the plastic under controlled temperature and pressure. Specialised features are key here:
- Degassing Vents: Double-vented extruders are essential for removing any remaining volatiles (including moisture) from the molten plastic, preventing bubbles and imperfections in the pellets.
- Filtrowanie: A screen changer filters out any final impurities from the melt before it proceeds to the cutting phase.
- Pelletising Head: The molten plastic is extruded through a die head into strands, which are then cut into pellets by a high-speed pelletiser, often under water for rapid cooling.
The result is a high-quality, homogenous pellet that commands a premium price and performs reliably in injection moulding or other manufacturing processes.
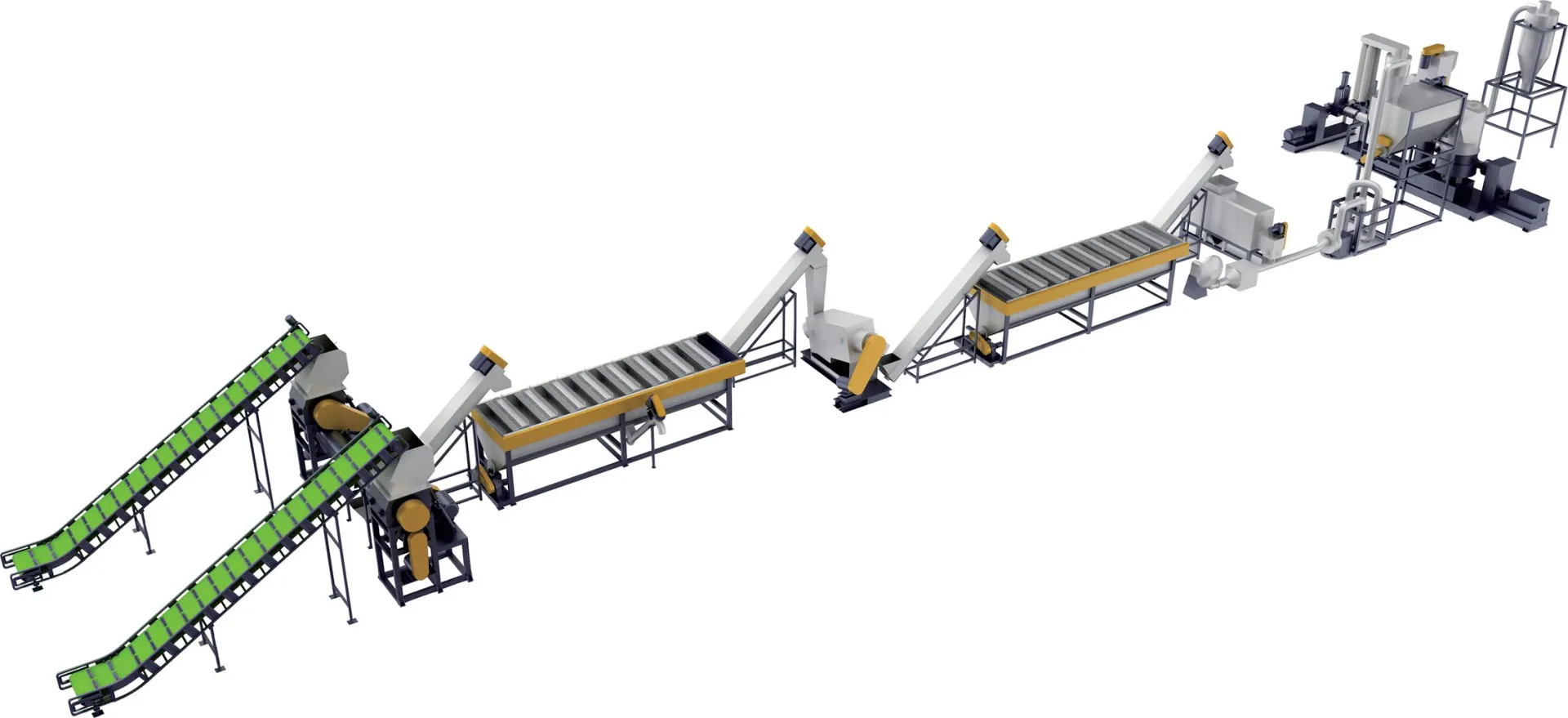
- [Bale Breaker] -> [Industrial Shredder] -> [Conveyor with Metal Detector] -> [Granulator] -> [High-Speed Friction Washer] -> [Float-Sink Tank] -> [Hot Washer] -> [Centrifugal Dryer] -> [Thermal Dryer] -> [Extruder/Pelletiser] -> [Vibrating Sieve] -> [Storage Silo for Pellets]
Choosing the Right Recycling Machine for 2025: Key Considerations
Selecting equipment is a long-term strategic decision. Here are the factors every professional buyer should analyse:
- Material Specificity: Is your primary input PET, HDPE, LDPE film, or rigid PP? The polymer’s characteristics (e.g., melting point, abrasiveness) dictate the ideal machine design, from the type of steel used for blades to the configuration of the extruder screw.
- Throughput & Capacity (kg/hr): Your required output determines the size and power of the machinery. It’s crucial to plan for future growth. A modular system, like those offered by Maszyna do rumu, allows you to scale your capacity as your business expands.
- Efektywność energetyczna: With rising energy costs in Europe and the USA, efficiency is paramount. Look for machines with high-efficiency motors (IE3/IE4), smart controls that power down idle components, and designs that minimise thermal loss. This directly impacts your operational expenditure.
- Automation and Integration: A fully integrated line with a central PLC control system reduces labour costs, minimises human error, and optimises the workflow. The ability for machines to “talk” to each other ensures a smooth, continuous process from shredder to pelletiser.
- Durability and Maintenance: Downtime is lost revenue. Prioritise machines built with high-quality, wear-resistant components. Easy access for maintenance, such as hydraulically opening chambers on granulators or easily replaceable screens, is a critical design feature.
Performance Comparison of Standard vs. Advanced Recycling Equipment
Metryczny | Standard Recycling Machine | Rumtoo Machine High-Performance System | Advantage |
---|---|---|---|
Final Product Purity | 95-97% | >99% | Higher market value, suitable for food-grade applications (with approvals). |
Zużycie energii | High (Older Motors, Poor Insulation) | Optimised (IE4 Motors, Smart Controls) | 15-25% lower operational costs. |
Throughput Consistency | Variable, Prone to Bottlenecks | Stable, PLC-controlled synchronised line | Predictable output, improved OEE (Overall Equipment Effectiveness). |
Przestój konserwacyjny | Frequent, Difficult Access | Scheduled, Easy Access Designs | Increased uptime and operational availability. |
Konsumpcja wody | High, Open-Loop System | Lower, with Water Filtration/Recirculation | Reduced environmental impact and utility costs. |
The Rumtoo Machine Advantage: Your Partner in Excellence
In a competitive market, your equipment supplier should be more than a vendor; they should be a partner. This is where Maszyna do rumu demonstrates its commitment to E-E-A-T (Experience, Expertise, Authoritativeness, and Trustworthiness).
- Experience & Expertise: We don’t offer one-size-fits-all solutions. Our engineers analyse your specific needs—your input materials, contamination levels, and output goals—to design a bespoke maszyna do recyklingu or a complete turnkey system.
- Authoritativeness & Trust: Our machines are built to exceed international standards (CE/ISO), ensuring safety, reliability, and performance. We stand behind our technology with robust warranties and responsive after-sales support, providing spare parts and technical assistance to keep your operation running smoothly. You can explore our full range of advanced recycling solutions to see how we tailor technology to meet specific industry needs. Our track record with leading manufacturers across Europe and the USA is a testament to our credibility.
Często zadawane pytania (FAQ)
1. What is the single biggest challenge in industrial plastic recycling today?
The primary challenge remains contamination. Mixed plastics, residual organic matter, and non-plastic materials can degrade the quality of the final product and damage machinery. This is why a sophisticated, multi-stage washing and separation line is absolutely essential for any serious recycling operation.
2. How do I decide between a shredder and a granulator?
Think of it as a primary vs. secondary reduction. A shredder is best for large, bulky, or heavily contaminated items (e.g., baled film, large drums) as a first step. A granulator is used to create a smaller, uniform flake from either shredded material or smaller, cleaner rigid parts. Many high-capacity lines use both.
3. Is a hot washing system always necessary?
For post-consumer PET bottles, yes, it is considered essential to remove glues and create high-purity rPET flakes. For cleaner, post-industrial scrap (e.g., PP off-cuts from manufacturing), a robust cold washing system may be sufficient. The experts at Maszyna do rumu can help you assess your material and determine the most cost-effective solution.
Conclusion: Future-Proof Your Operations Today
The transition toward a circular economy is accelerating, and 2025 stands as a key milestone. For manufacturers and industrial recyclers, this represents a profound opportunity. By moving beyond basic recycling and embracing advanced, integrated systems, you can transform plastic waste from a liability into a valuable, profitable resource.
The key is a strategic investment in the right technology—equipment that delivers purity, efficiency, and reliability. A well-designed line, featuring a high-performance recycling machine at each critical stage, is the engine of a successful modern recycling enterprise.
Ready to elevate your plastic recycling capabilities and meet the demands of 2025?
The technical team at Maszyna do rumu is ready to help you design the perfect system for your business.
Contact us today for a personalised consultation or to request a detailed quote for your project.