Advantages of Densification in Recycling
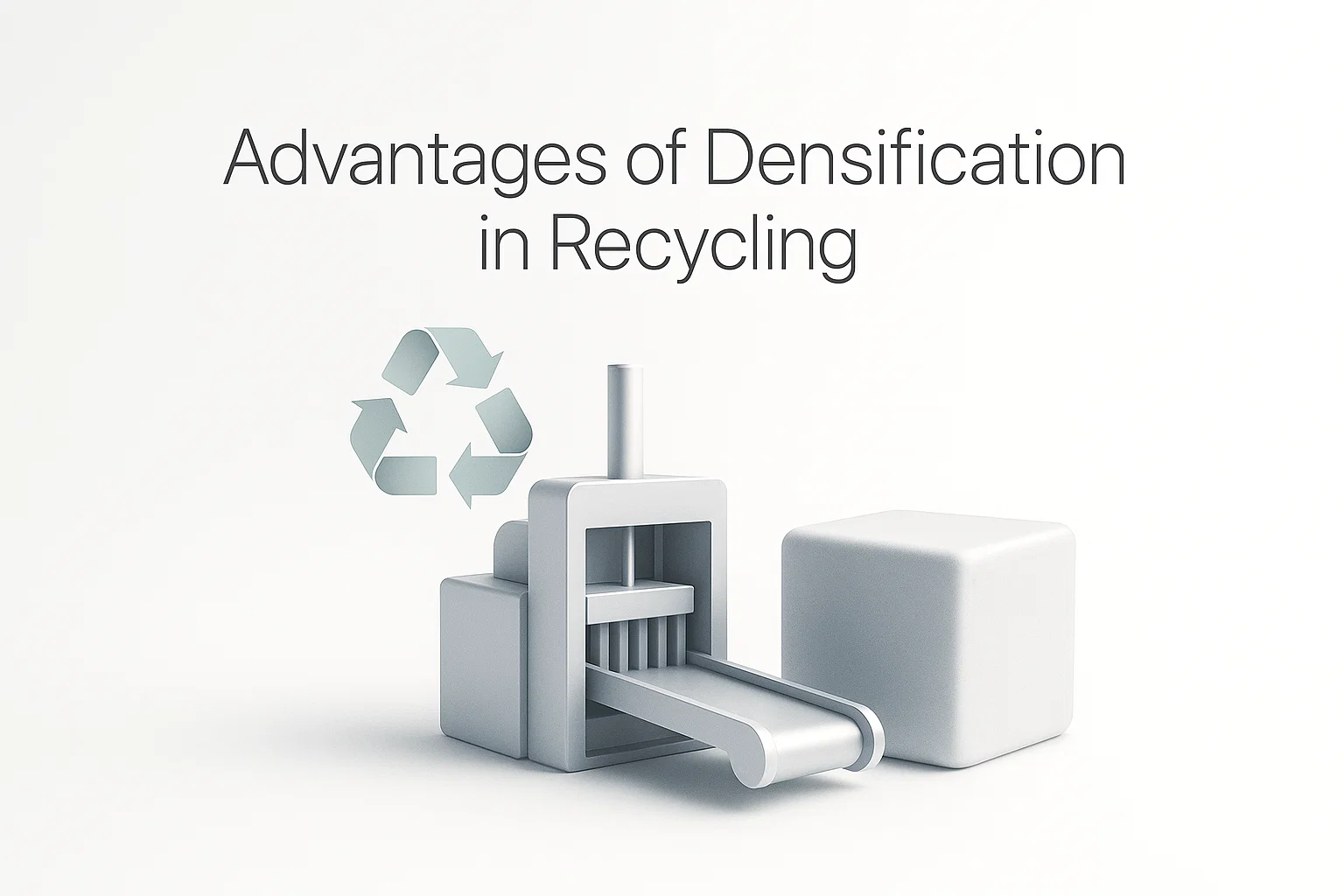
In the ever-growing challenge of managing plastic waste, densification emerges as a pivotal process in the recycling industry. As global plastic production surpasses 400 million tons annually, effective recycling methods are cruci...