Vertical Mixing and Drying Machine is a versatile piece of industrial equipment designed to perform both mixing and drying functions in various manufacturing processes. Here are some key features and applications of this type of machinery:
Key Features:
1. Design: The machine typically features a vertical, cylindrical tank with a conical bottom. This design helps in the efficient mixing and drying of materials. The vertical orientation ensures a smaller footprint, making it suitable for facilities with limited space.
2. Materials: Constructed from high-grade stainless steel or other corrosion-resistant materials, it ensures durability and resistance to various chemicals, making it ideal for use in harsh industrial environments.
3. Heating and Cooling Systems: Many vertical mixers come equipped with integrated heating systems. These can be used to control the temperature during the mixing process, which is critical for processing temperature-sensitive materials.
4. Control System: Equipped with advanced control panels that allow operators to set and monitor various parameters such as temperature, mixing speed, and time. This enhances precision and repeatability in processes.
5. Safety Features: Safety mechanisms, such as emergency stop buttons and safety interlocks on access doors, are commonly included to protect operators and the machinery itself.
6. Accessories: Optional attachments, like spray nozzles for liquid addition or vacuum systems for deaeration, can be included to enhance functionality.
Technical Parameter:
Name | Specification |
---|---|
Volume | 3000L |
Power | 4kW |
Heating Power | 42kW |
Fan or Blower | 2.2kW |
Plate Thickness | 2.5mm |
Spindle Specifications | φ60×4 |
Blade Thickness | 3mm |
Screw Diameter | φ273 |
Equipment Weight | 700kg |
Dimensions | L1900xW2300xH3100 |
Applications:
• Chemical Industry: Used for mixing and drying chemical compounds, ensuring thorough blending and moisture removal.
• Food and Beverage: Suitable for mixing spices, powders, and other food ingredients while removing moisture to achieve desired consistency and preservation.
• Pharmaceuticals: Utilized for the homogeneous mixing of drug ingredients, ensuring consistent batch quality, and drying them to required moisture levels.
• Cosmetics: Used for blending various powders and granules used in cosmetic products, ensuring uniform texture and composition.
Benefits:
• Efficiency: Combines two processes into one machine, reducing processing time and improving throughput.
• Quality Control: Ensures consistent quality and homogeneity of the final product, critical in industries where composition directly affects performance.
• Energy Saving: Many designs focus on energy efficiency, which can significantly reduce operational costs over time.
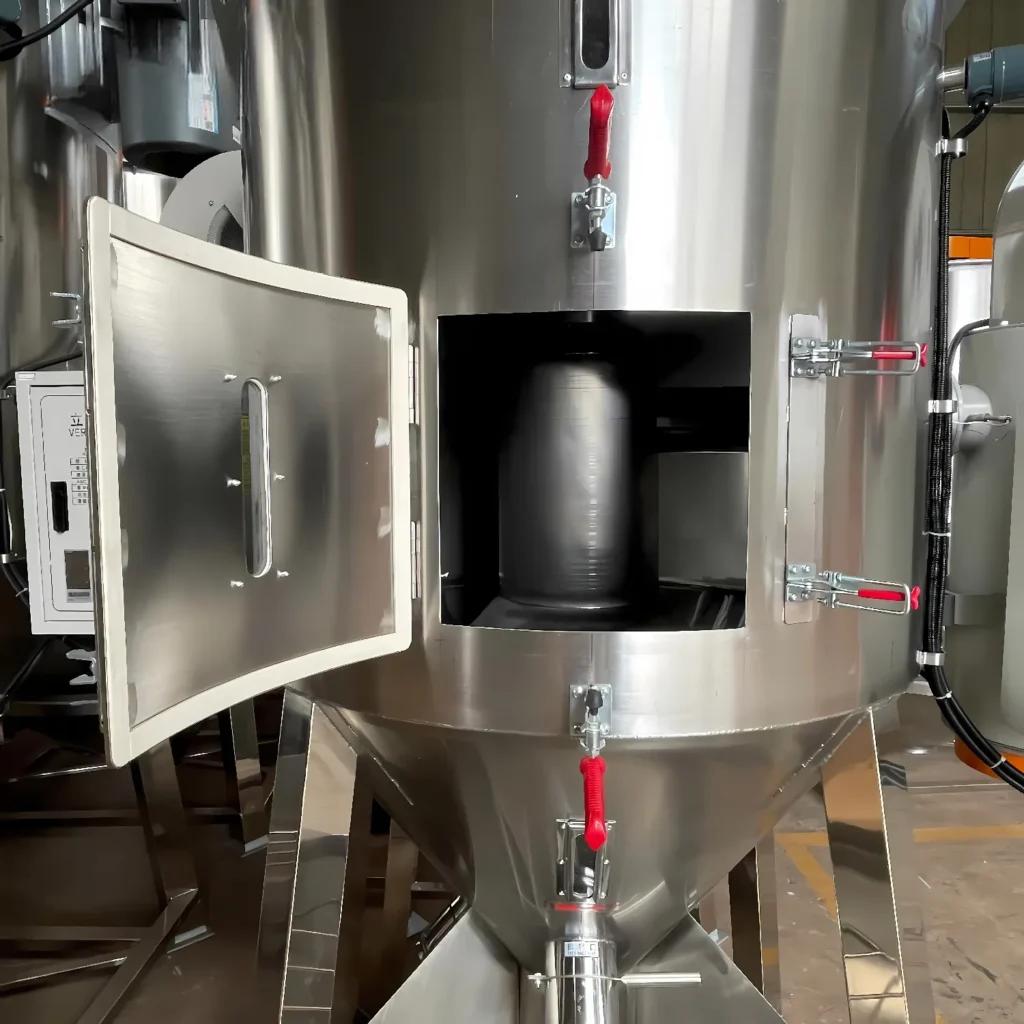
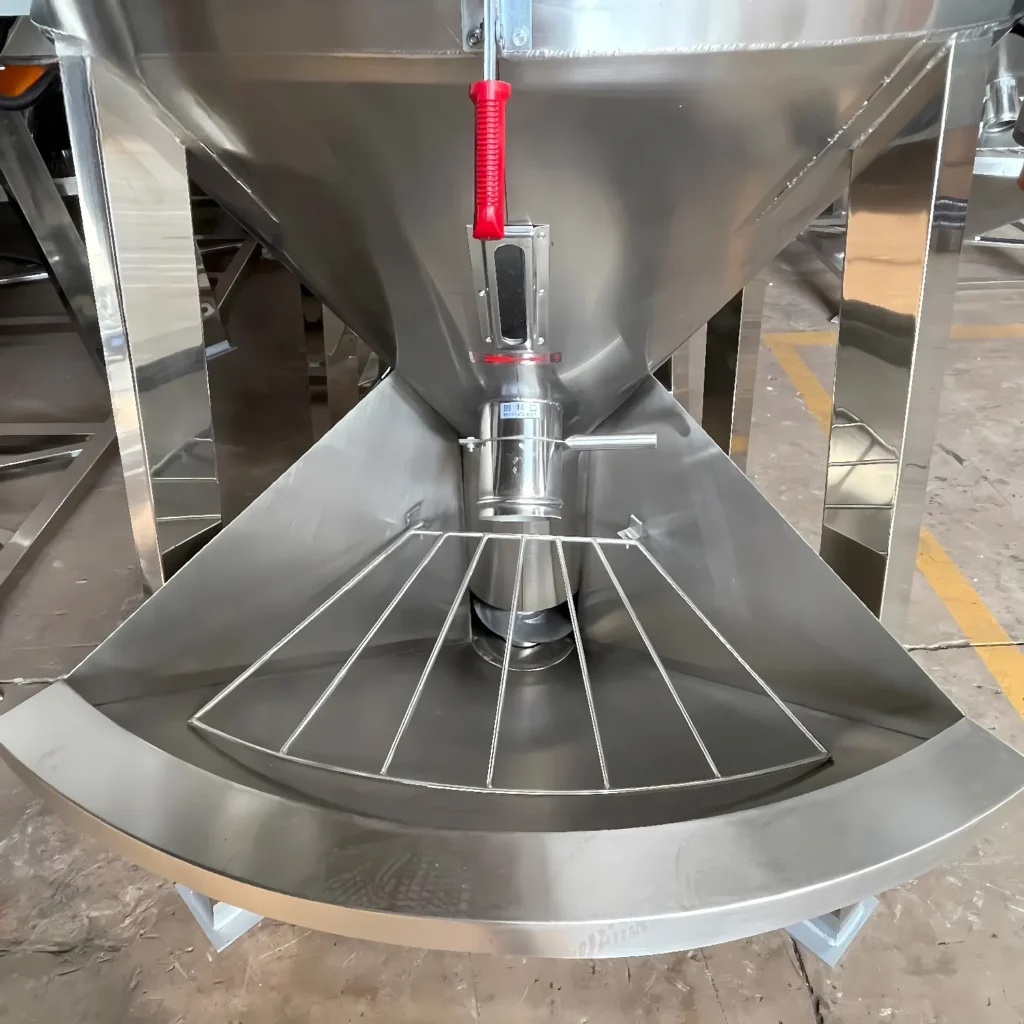
Maintenance and Care:
Regular maintenance is crucial for ensuring longevity and performance. This includes routine checks and cleaning, lubrication of moving parts, inspection of heating elements, and calibration of control systems.
Contact us today to learn more about how we can customize a solution to meet your specific needs and help you achieve optimal efficiency and profitability.