Расшифровка важнейших инструментов в операциях по переработке отходов
In the fast-paced world of recycling, where efficiency meets innovation, the spotlight often lands on two heavyweight champions: plastic granulators and plastic crushers. As the push for sustainability gains momentum, understanding the roles and differences of these devices is not just useful—it's essential. Let's break down what these machines do, why they're important, and how they differ.
In recent years, the recycling industry has witnessed a surge of innovations in plastic granulators that are transforming the way we process and recycle plastic waste. These cutting-edge advancements are not only improving the efficiency and performance of granulators but also contributing to a more sustainable future. In this article, we will explore some of the most significant innovations in plastic granulators and how they are revolutionizing the recycling industry.
The Importance of Грануляторы для пластмасс in Recycling
Plastic granulators play a crucial role in the recycling process by reducing large plastic waste into smaller, more manageable pieces known as granules. These granules can then be easily sorted, cleaned, and reprocessed into new plastic products. Granulators are essential for efficiently handling the ever-growing amount of plastic waste generated by our society.
The Need for Innovation in Plastic Granulators
As the demand for recycled plastic increases, so does the need for more advanced and efficient plastic granulators. Traditional granulators often face challenges such as high noise levels, energy consumption, and maintenance requirements. Additionally, the increasing complexity of plastic waste streams requires granulators to adapt and handle a wider range of materials effectively.
Noise Reduction Technologies
One of the most significant advancements in plastic granulators is the development of noise reduction technologies. Granulators are known for their high noise levels, which can be a concern for workers and neighboring communities. However, innovative designs and materials are now being used to minimize noise pollution.
Soundproofing Materials and Enclosures
Manufacturers are incorporating soundproofing materials, such as acoustic foams and insulation, into the construction of granulators. These materials absorb and dampen sound waves, significantly reducing the noise emitted by the machines. Additionally, some granulators are equipped with soundproof enclosures that further contain the noise, creating a quieter working environment.
Optimized Rotor Designs
The design of the granulator rotor plays a crucial role in noise generation. Innovative rotor designs, such as helical and staggered blade configurations, help reduce noise by minimizing turbulence and vibrations. These optimized designs not only contribute to noise reduction but also improve the overall performance and efficiency of the granulator.
Energy Efficiency Improvements
Another area where plastic granulators are seeing significant advancements is energy efficiency. As the recycling industry strives to reduce its environmental impact, manufacturers are developing granulators that consume less energy without compromising performance.
High-Efficiency Motors
The integration of high-efficiency motors is one of the key innovations in energy-efficient granulators. These motors consume less electricity while delivering the same or even better performance compared to traditional motors. By reducing energy consumption, recycling facilities can lower their operating costs and minimize their carbon footprint.
Optimized Cutting Chamber Designs
The design of the cutting chamber also plays a vital role in energy efficiency. Innovative designs, such as optimized blade angles and cutting geometries, enable granulators to process plastic waste more efficiently. These improvements reduce the amount of energy required to achieve the desired granule size, resulting in significant energy savings.
Smart Monitoring Systems
The integration of smart monitoring systems is another game-changing innovation in plastic granulators. These systems utilize sensors, data analytics, and connectivity to provide real-time insights into the performance and health of the granulator.
Predictive Maintenance
Smart monitoring systems can detect potential issues before they lead to breakdowns or failures. By analyzing data from sensors that monitor vibration, temperature, and other parameters, these systems can predict when maintenance is required. This predictive maintenance approach minimizes downtime, extends the lifespan of the granulator, and reduces overall maintenance costs.
Remote Monitoring and Control
With the advent of Internet of Things (IoT) technology, plastic granulators can now be remotely monitored and controlled. Operators can access real-time data, adjust settings, and receive alerts from anywhere, enabling them to optimize the granulator's performance and respond quickly to any issues. This level of connectivity and control enhances the efficiency and flexibility of recycling operations.
The Impact of Granulator Innovations on the Recycling Industry
The innovations in пластиковые грануляторы are having a profound impact on the recycling industry. By improving efficiency, reducing noise and energy consumption, and enabling predictive maintenance, these advancements are making the recycling process more sustainable and cost-effective.
Increased Recycling Capacity
With more efficient and reliable granulators, recycling facilities can process larger volumes of plastic waste in less time. This increased capacity helps keep pace with the growing demand for recycled plastic and contributes to the overall growth of the recycling industry.
Reduced Environmental Impact
The energy efficiency improvements and noise reduction technologies in modern granulators are significantly reducing the environmental impact of plastic recycling. By consuming less energy and minimizing noise pollution, these innovations are making the recycling process more sustainable and environmentally friendly.
Enhanced Profitability
The cost savings achieved through energy efficiency, predictive maintenance, and increased recycling capacity are boosting the profitability of recycling operations. As granulators become more efficient and reliable, recycling facilities can optimize their processes, reduce operating costs, and improve their bottom line.
Заключение
The innovations in plastic granulators are revolutionizing the recycling industry by addressing key challenges and improving the efficiency, sustainability, and profitability of plastic recycling. From noise reduction technologies and energy-efficient designs to smart monitoring systems, these advancements are transforming the way we process and recycle plastic waste. As the demand for recycled plastic continues to grow, the adoption of innovative granulators will be crucial in building a more sustainable future.
Frequently Asked Questions (FAQs)
- What are the benefits of noise reduction technologies in plastic granulators?
Noise reduction technologies, such as soundproofing materials and optimized rotor designs, help create a quieter working environment, reduce noise pollution, and improve worker comfort and safety. - How do energy-efficient granulators reduce operating costs?
Energy-efficient granulators, equipped with high-efficiency motors and optimized cutting chamber designs, consume less electricity while maintaining high performance. This reduction in energy consumption leads to lower operating costs for recycling facilities. - What is predictive maintenance, and how does it benefit recycling operations?
Predictive maintenance involves using smart monitoring systems to detect potential issues before they lead to breakdowns or failures. By predicting when maintenance is required, recycling facilities can minimize downtime, extend the lifespan of their granulators, and reduce overall maintenance costs. - How do smart monitoring systems enhance the efficiency of plastic granulators?
Smart monitoring systems provide real-time data and insights into the performance and health of plastic granulators. This allows operators to optimize settings, respond quickly to issues, and make data-driven decisions to improve efficiency and productivity. - What role do innovative plastic granulators play in building a more sustainable future?
Innovative plastic granulators contribute to a more sustainable future by increasing recycling capacity, reducing energy consumption, and minimizing the environmental impact of plastic recycling. By making the recycling process more efficient and cost-effective, these advancements encourage the adoption of recycling practices and support the transition towards a circular economy.
Plastic granulators are essential machines in the plastic recycling process, breaking down plastic waste into small, uniform granules that can be reused in the production of new plastic products. To ensure that your пластиковый гранулятор operates efficiently and has a long lifespan, it's crucial to implement a proper maintenance routine and troubleshoot any issues that may arise.
In this comprehensive guide, we'll walk you through the essential steps for maintaining your plastic granulator, troubleshooting common problems, and optimizing its performance to extend its operational life.
Why Proper Maintenance is Essential for Your Plastic Granulator
Regular maintenance of your пластиковый гранулятор is crucial for several reasons:
- Ensuring optimal performance and efficiency
- Preventing unexpected breakdowns and costly repairs
- Extending the lifespan of the machine
- Maintaining the quality and consistency of the granules produced
By implementing a proper maintenance routine, you can keep your plastic granulator running smoothly and avoid disruptions to your recycling process.
Essential Maintenance Tasks for Your Plastic Granulator
To keep your пластиковый гранулятор in top condition, perform the following maintenance tasks regularly:
1. Daily Maintenance
- Clean the hopper and feed area to prevent blockages
- Check the cutting chamber for any debris or buildup
- Inspect the blades and screens for wear or damage
- Lubricate moving parts as per the manufacturer's recommendations
2. Weekly Maintenance
- Clean the air filter to ensure proper airflow and cooling
- Check the condition of the drive belts and replace if necessary
- Inspect the electrical connections and tighten any loose wires
- Clean the exterior of the machine to prevent dust and debris accumulation
3. Monthly Maintenance
- Check the alignment of the rotor and stator
- Inspect the bearings for wear and replace if necessary
- Clean and lubricate the gearbox
- Test the safety features, such as emergency stop buttons and interlocks
4. Annual Maintenance
- Perform a complete overhaul of the machine
- Replace worn parts, such as blades, screens, and bearings
- Recalibrate the machine to ensure optimal performance
- Update the machine's software and firmware, if applicable
Troubleshooting Common Issues with Your Plastic Granulator
Despite regular maintenance, issues may still arise with your plastic granulator. Here are some common problems and their potential solutions:
1. Granulator Not Starting
- Check the power supply and electrical connections
- Inspect the safety switches and interlocks
- Verify that the emergency stop button is not engaged
2. Reduced Granule Output
- Check for dull or damaged blades and replace if necessary
- Inspect the screens for blockages or damage
- Verify that the feed rate is appropriate for the machine's capacity
3. Inconsistent Granule Size
- Check the condition of the blades and screens and replace if worn
- Verify that the rotor and stator are properly aligned
- Ensure that the feed material is consistent in size and composition
4. Excessive Noise or Vibration
- Check for loose or worn bearings and replace if necessary
- Inspect the rotor and stator for damage or imbalance
- Verify that the machine is properly leveled and anchored
Optimizing Your Plastic Granulator's Performance
To get the most out of your plastic granulator and extend its lifespan, consider the following optimization tips:
1. Use the Right Blades and Screens
Select blades and screens that are appropriate for the type and thickness of the plastic waste you're processing. Using the wrong components can lead to reduced efficiency and increased wear and tear on the machine.
2. Maintain a Consistent Feed Rate
Ensure that the plastic waste is fed into the granulator at a consistent rate to avoid overloading the machine and causing unnecessary strain on its components.
3. Monitor Power Consumption
Keep an eye on the granulator's power consumption, as an increase in power draw may indicate a problem, such as dull blades or a clogged screen.
4. Implement Predictive Maintenance
Use sensors and monitoring systems to track the performance of your plastic granulator and predict when maintenance tasks or component replacements will be necessary. This can help you avoid unexpected breakdowns and schedule maintenance during planned downtime.
Заключение
Maintaining and extending the lifespan of your plastic granulator is essential for ensuring efficient and cost-effective переработка пластика. By implementing a proper maintenance routine, troubleshooting common issues, and optimizing your granulator's performance, you can keep your machine running smoothly and avoid costly repairs or replacements.
Remember to follow the manufacturer's recommendations for maintenance and always prioritize the safety of your operators by providing proper training and ensuring that all safety features are functioning correctly.
Frequently Asked Questions (FAQs)
- Q: How often should I sharpen or replace the blades on my plastic granulator?
A: The frequency of blade sharpening or replacement depends on factors such as the type and volume of plastic waste being processed and the hardness of the blades. On average, blades may need to be sharpened every 100-300 hours of operation and replaced every 500-1,000 hours. - Q: Can I use aftermarket or generic replacement parts for my plastic granulator?
A: While aftermarket or generic replacement parts may be less expensive, it's generally recommended to use original equipment manufacturer (OEM) parts to ensure compatibility, performance, and safety. Using non-OEM parts may void your machine's warranty and lead to reduced efficiency or premature wear. - Q: How can I train my operators to properly maintain and troubleshoot the plastic granulator?
A: Provide thorough training to your operators, covering topics such as daily maintenance tasks, safety procedures, and common troubleshooting techniques. Develop a clear maintenance checklist and ensure that all operators follow it consistently. Encourage open communication and have experienced technicians mentor new operators. - Q: What should I do if my plastic granulator experiences a sudden breakdown?
A: In the event of a sudden breakdown, first ensure that all operators are safe and that the machine is properly shut down. Diagnose the issue using the troubleshooting guide provided by the manufacturer or consult with a qualified technician. If necessary, contact the manufacturer's customer support for assistance or to order replacement parts. - Q: How can I dispose of the dust and fines generated during the granulation process?
A: The dust and fines generated during plastic granulation can be collected using a dust collection system or air filtration unit. Properly dispose of this waste in accordance with local environmental regulations, as it may contain additives or contaminants that require special handling. In some cases, the dust and fines can be reused in certain applications or sold to other industries for use as fillers or additives.
In today's world, where plastic waste is a growing concern, recycling has become more crucial than ever. One of the key components in the plastic recycling process is the granulator, a machine that breaks down plastic waste into smaller, more manageable pieces called granules. These granules can then be reused to create new plastic products, reducing the need for virgin plastic and minimizing the environmental impact of plastic waste.
However, not all plastic granulators are created equal. There are various types of granulators designed to handle different kinds of plastic waste and cater to specific recycling needs. In this article, we'll explore the different types of plastic granulators and help you determine which one suits your recycling needs best.
Reaching new heights! On the opening day, 93,241 elites parachuted in, surging by 34.66%! The domineering return show of CHINAPLAS ignited Shanghai!
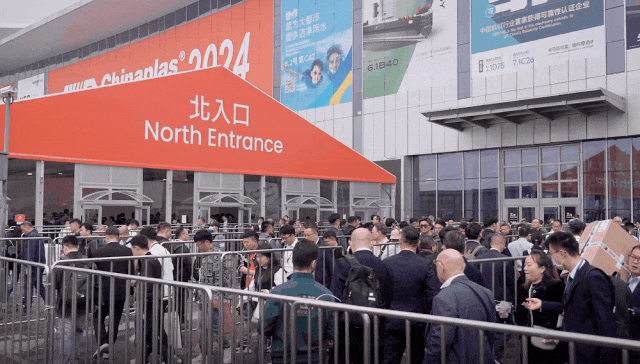
CHINAPLAS 2024 witnessed a record-breaking attendance of 93,241 visitors on its opening day, including 19,380 from overseas, setting a new high for the daily number of international guests.
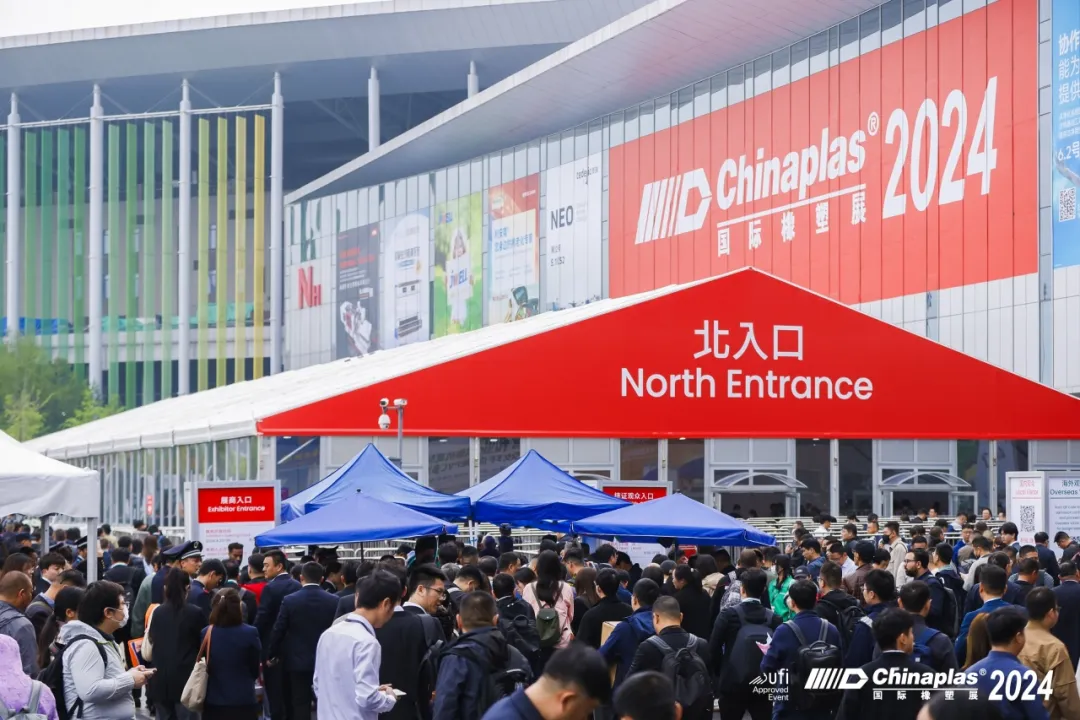
As the iconic exhibition progresses into its second day, a plethora of plastic and rubber technologies are on display. Among these, solutions that offer cost savings and high efficiency are particularly captivating for attendees.
In the prevailing global economic landscape, it is crucial for manufacturers to embrace cost-saving production strategies to enhance competitive advantage, increase flexibility, boost profitability, and promote sustainability.
Manufacturers who adopt such strategies can deliver products or services at reduced prices without compromising quality, potentially capturing a larger market share and increasing profit margins.
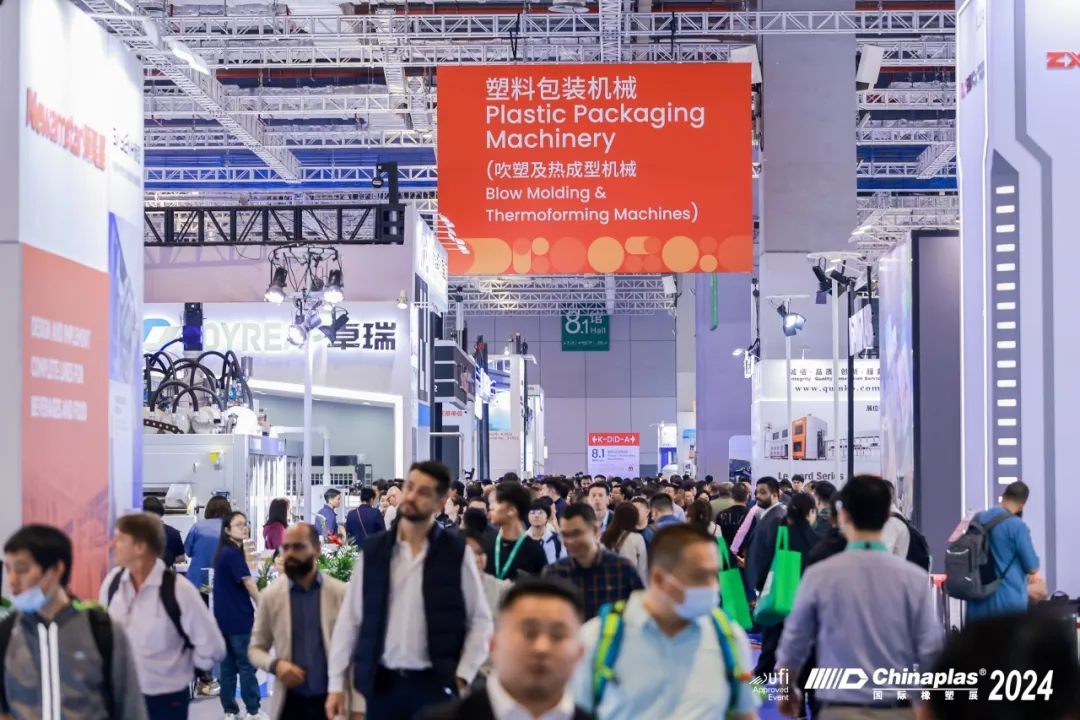

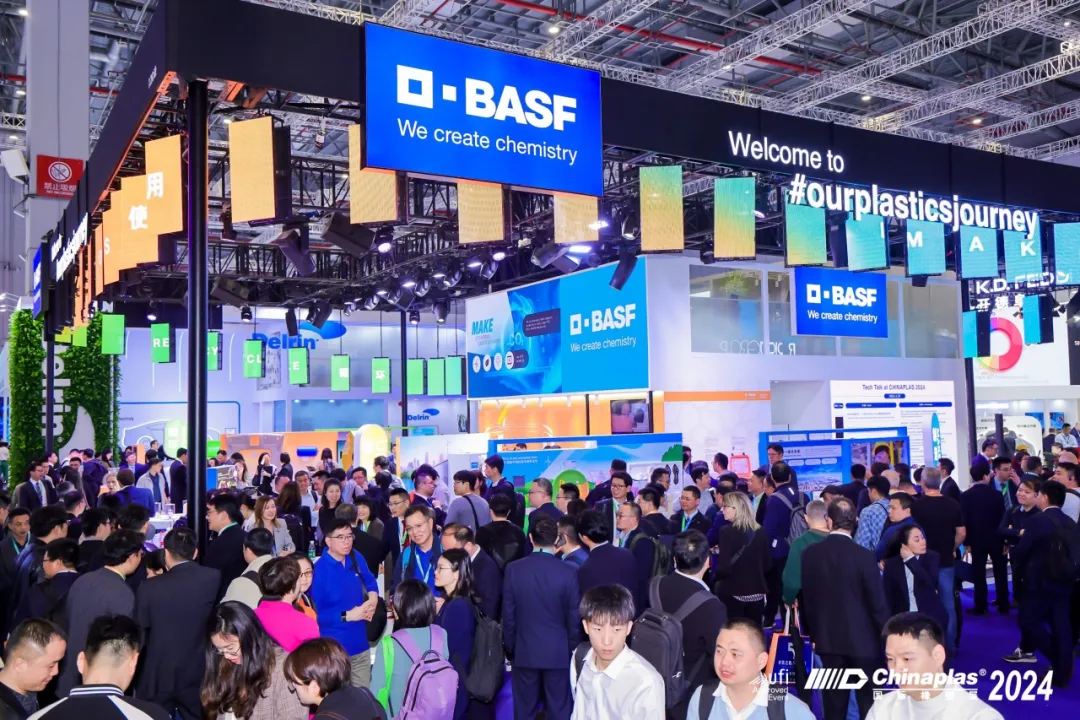
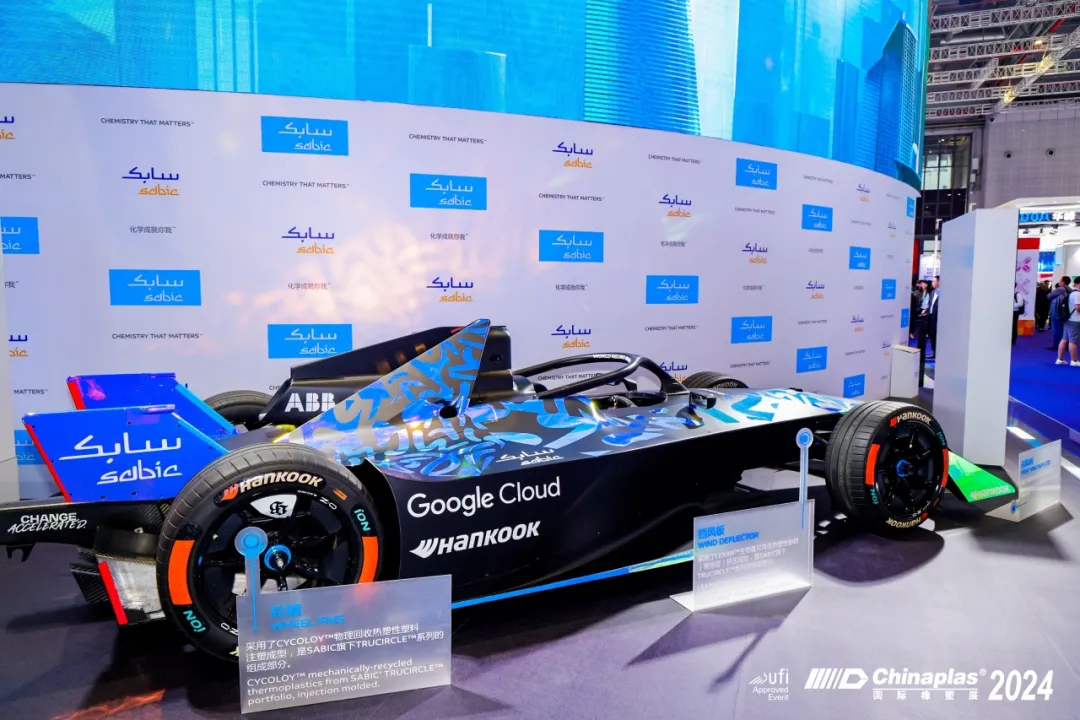
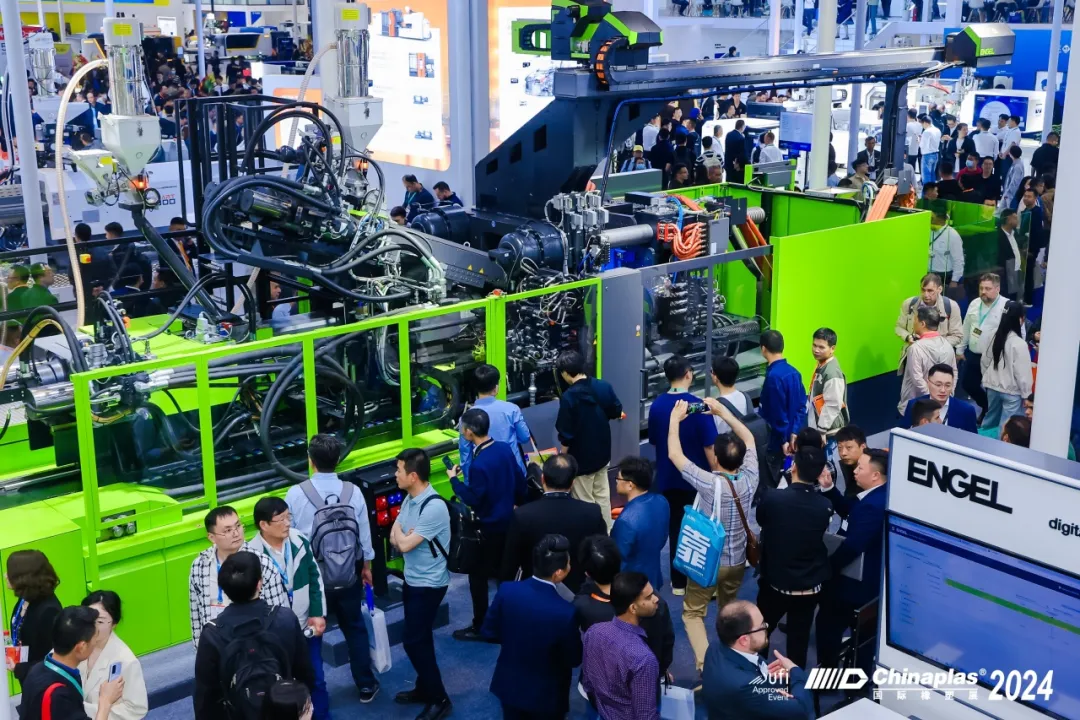
Recently, "new productivity" has surged in popularity, with nearly ten emerging and future-focused industries drawing significant attention. These sectors, including new energy vehicles, emerging hydrogen energy, new materials, innovative medicines, biomanufacturing, commercial aerospace, and the low-altitude economy, are thriving with limitless innovations. For instance, in 2023, China's new energy vehicle industry saw a year-on-year increase of 35.8% in production and 37.9% in sales, with exports rising by 67.1%, claiming over 60% of the global market share.
Behind this wave of industrial innovation lies crucial support from upstream suppliers, including advancements in new plastics and rubber materials, equipment, and processes. At CHINAPLAS 2024, visitors are introduced to an array of cutting-edge technologies that push the boundaries of downstream applications. Innovations on display include specialized silicone elastomers for new energy vehicles, materials that enhance lightweighting, efficient thermal management, and recyclability in solid-state battery packs, and halogen-free flame-retardant reinforced PA66 used in high-voltage connectors. Additionally, technologies like POE and silane-grafted olefin polymers, light stabilizers for photovoltaic adhesive films, ETFE films to boost photovoltaic module efficiency, solar automatic dies, medical-grade PLA and PEEK 3D filament extrusion equipment, biodegradable bone nail injection molding technology, customized recycling solutions for packaging, PHA special modified materials, and high-strength materials for use in aerospace, aviation, and rail transportation, are showcased.
The exhibition hosts over 3,800 machinery exhibits, more than 1,500 raw material suppliers, and 200 debuts of global and Asian technologies, making it a premier platform for groundbreaking technologies. Concurrently, the World Trends and Plastics and Rubber Technology Summit attracts visitors with its focus on artificial intelligence, the internet of things, photovoltaic and wind power, green hydrogen storage, new energy vehicles, and lithium battery technology. Discussions explore major trends, opportunities, and challenges in the global plastics and rubber industries, digitalization for industrial transformation and sustainability, innovative technologies for electric vehicles, and green energy.
The Tech Talk segment highlights five main themes: Eco-friendly Solutions, Advanced Packaging Solutions, Automotive Plastic Solutions, 3D Printing, and New Materials for 2024, unveiling over 30 of the latest and most revolutionary technologies. Additionally, the Application in Focus sessions feature 10 thematic seminars covering over 60 topical issues such as photoelectric cables, low-carbon energy, medical sterilization packaging, integrated biomedical engineering, ready-meal packaging, automobile safety, and environmental protection.
This year's exhibition emphasizes "Circular Economy," "Innovative Materials," "Digitalization," and "High-end Technologies from China," showcasing collaborations with leading exhibitors to present state-of-the-art innovations and demonstrate the advancement and "new productive forces" of the plastics and rubber industries. Efforts are focused on fostering collaborative innovation among upstream and downstream sectors to accelerate the development of these "new productive forces."
The exhibition's 17 theme zones highlight eco-friendly manufacturing initiatives, such as the Recycling Technology Zone, Bioplastics Zone, and Recycled Plastics Zone, aiming to explore the vast potential of the circular economy. Technologies on display include 90% post-consumer recycled polycarbonate, mass-balanced PA66 incorporating Asian post-consumer plastic waste, chemically recycled medical-grade ABS materials, sustainable TPE, bottle flake sorting machines, and more.
Material innovation continues to drive technological breakthroughs and upgrades across various industries. With over 1,500 raw material suppliers, the exhibition features a wide range of innovative materials, including the world's first PA12 powder for 3D printing derived from biologically recycled materials, non-food bottle caps made from post-consumer recycled PP plastic, inorganic antibacterial additives, graphene masterbatch, and more.
In the digital economy theme zones, visitors discover innovative solutions encompassing machine learning, artificial intelligence, mold monitoring, data and image monitoring, vision inspection systems, fully servo-automatic blow molding, system integration, collaborative robots, modular design systems, solutions for automated interconnection of multiple production processes, in-mold painting technology, upgraded versions of high-speed, highly stable robotic arms, and turnkey solutions for highly integrated medical pipette tips.
Local enterprises play a significant role, with over 800 Chinese companies recognized as "Technologically Advanced Small and Medium-sized Enterprises" and more than 250 awarded as "Little Giants." They showcase innovations such as two-plate intelligent injection molding machines, high-speed precision injection molding machines, and cutting-edge 56-layer nano-wrap film production lines, demonstrating "High-end Technologies from China" to the global audience.
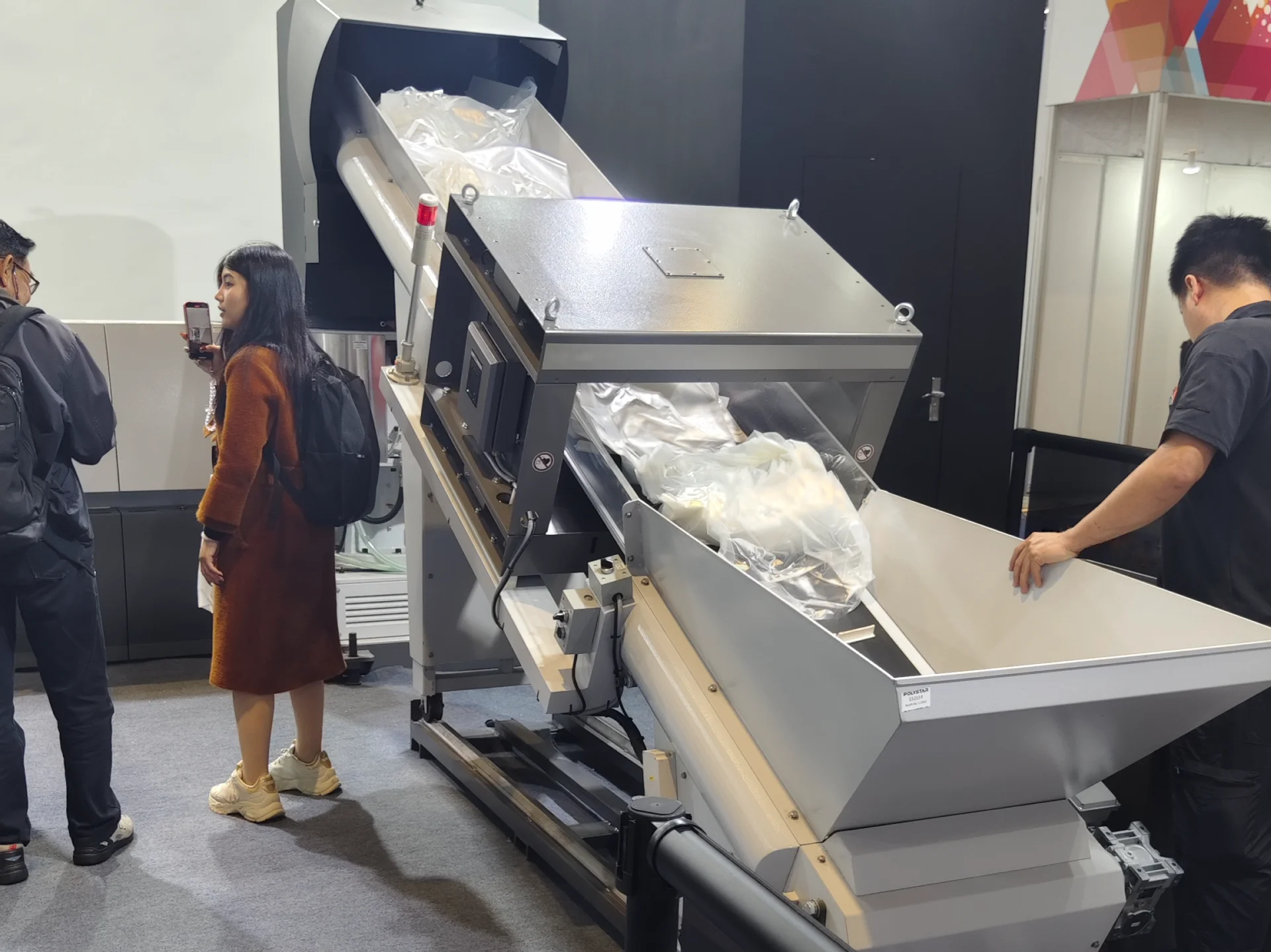
The Plastics Recycling & Circular Economy Conference and Showcase, held on April 22, gathered over 1,000 industry leaders who shared insights on "Переработка пластика and Fashion Trends," "Recycling and New Plastics Economy," and "Industrial Linkage and Low Carbon in All Fields."