Prodaja stroja za recikliranje plastike: Pametna investicija za održivu budućnost
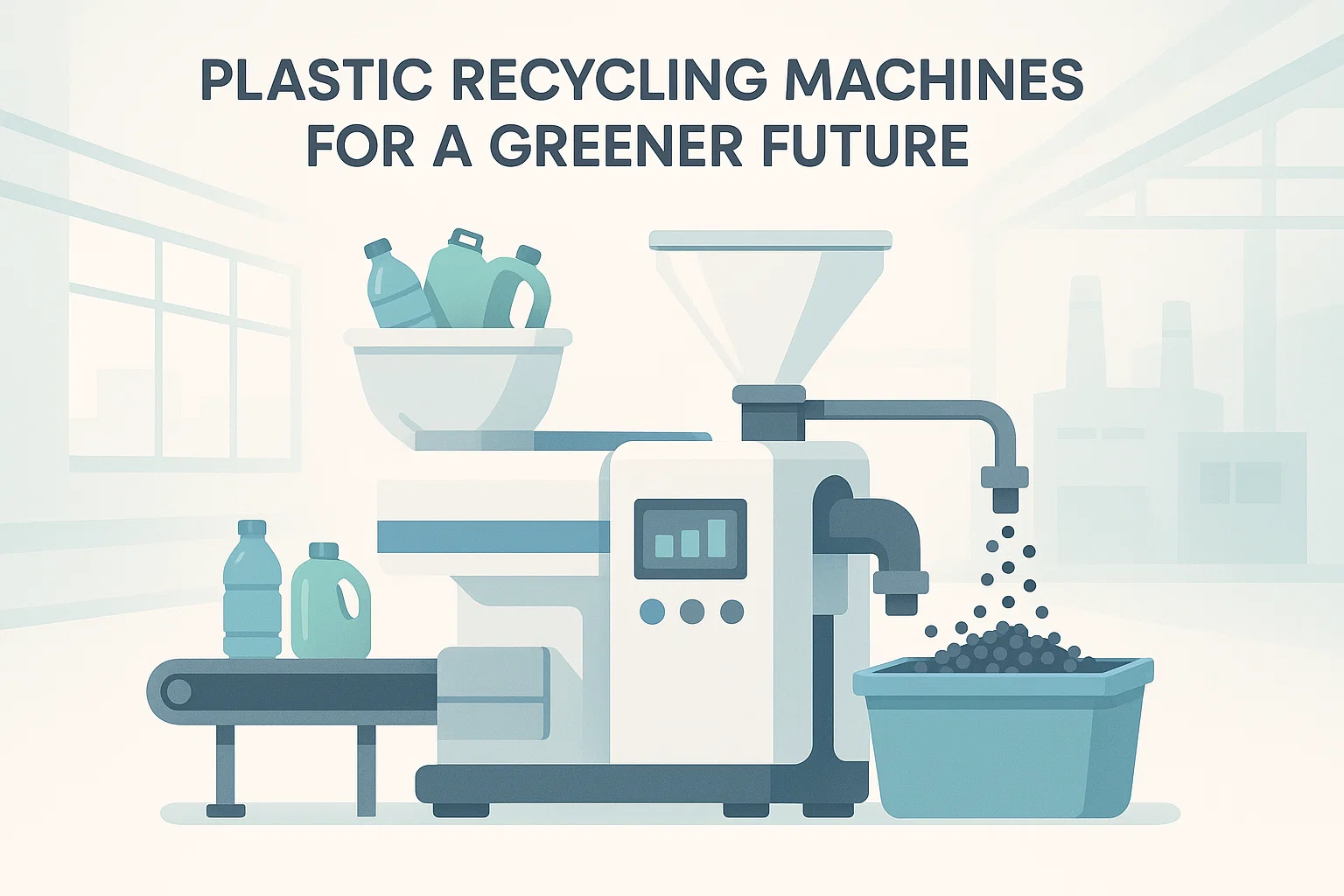
U eri u kojoj održivost više nije opcionalna, ulaganje u visokokvalitetne strojeve za recikliranje ključno je za tvrtke koje žele smanjiti svoj utjecaj na okoliš. U Rumtoo Machine specijalizirani smo za dizajn, upravljanje...